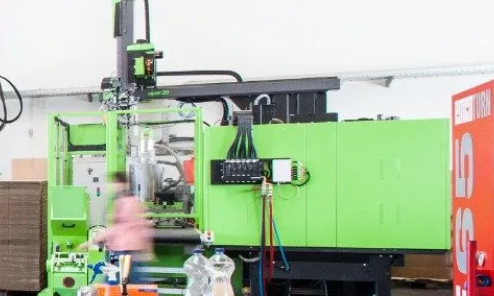
Die Verwendung von Farbstoffen und Additiven im Spritzguss
Wie Sie die Qualität und das Aussehen Ihrer Kunststoffprodukte verbessern können
Einleitung
- Was ist Spritzguss und warum ist es wichtig?
- Welche Vorteile haben Farbstoffe und Additive für Spritzgussteile?
- Wie wählt man die richtigen Farbstoffe und Additive aus?
Farbstoffe für Spritzguss
- Die verschiedenen Arten von Farbstoffen: Masterbatch, Flüssigfarbe, Pulver, Granulat
- Die Vor- und Nachteile der verschiedenen Farbstoffe
- Die wichtigsten Faktoren, die die Farbwirkung beeinflussen: Temperatur, Druck, Schmelzindex, Scherung, Form
- Die häufigsten Farbprobleme und wie man sie vermeidet: Verfärbung, Streifen, Flecken, Verblassen, Migration
Additive für Spritzguss
- Die verschiedenen Arten von Additiven: Stabilisatoren, Antioxidantien, Gleitmittel, Antistatika, Flammschutzmittel, UV-Schutzmittel, Biokompatibilitätsmittel, Verstärkungsmittel, Füllstoffe
- Die Vor- und Nachteile der verschiedenen Additive
- Die wichtigsten Faktoren, die die Additivwirkung beeinflussen: Dosierung, Kompatibilität, Verteilung, Wechselwirkung, Alterung
- Die häufigsten Additivprobleme und wie man sie vermeidet: Verlust der mechanischen Eigenschaften, Veränderung der Oberflächenqualität, Geruch, Geschmack, Toxizität, Umweltverträglichkeit
Fazit
- Zusammenfassung der wichtigsten Erkenntnisse und Empfehlungen
- Ausblick auf zukünftige Trends und Entwicklungen im Bereich der Farbstoffe und Additive für Spritzguss
- Aufforderung zum Handeln und Kontaktmöglichkeit
Einleitung
- Was ist Spritzguss und warum ist es wichtig?
Spritzguss ist ein Verfahren zur Herstellung von Kunststoffteilen, bei dem geschmolzener Kunststoff in eine Form gespritzt wird, die die gewünschte Form und Größe hat. Nachdem der Kunststoff abgekühlt und ausgehärtet ist, wird das Teil aus der Form entnommen. Spritzguss ist ein wichtiges Verfahren, weil es eine schnelle, effiziente und kostengünstige Möglichkeit ist, hochwertige Teile in großen Mengen zu produzieren. Spritzgussteile werden in vielen Branchen verwendet, wie z. B. Automobil, Medizin, Elektronik, Spielzeug und Verpackung. Spritzguss ermöglicht es, komplexe und präzise Teile mit minimaler Verschwendung und Umweltbelastung herzustellen.
- Welche Vorteile haben Farbstoffe und Additive für Spritzgussteile?
Farbstoffe und Additive für Spritzgussteile haben verschiedene Vorteile, je nach dem gewünschten Effekt und der Anwendung. Farbstoffe können die ästhetischen Eigenschaften von Kunststoffteilen verbessern, indem sie ihnen eine bestimmte Farbe, Glanz oder Transparenz verleihen. Farbstoffe können auch die Funktion von Kunststoffteilen beeinflussen, indem sie ihre Sichtbarkeit, UV-Beständigkeit oder Temperaturtoleranz erhöhen. Additive können die mechanischen, chemischen oder physikalischen Eigenschaften von Kunststoffteilen verbessern, indem sie ihre Festigkeit, Zähigkeit, Fließfähigkeit oder Stabilität erhöhen. Additive können auch die Leistung von Kunststoffteilen verbessern, indem sie ihnen antibakterielle, antistatische, flammhemmende oder gleitfähige Eigenschaften verleihen. Farbstoffe und Additive können also die Qualität, Vielfalt und Funktionalität von Spritzgussteilen erhöhen.
- Wie wählt man die richtigen Farbstoffe und Additive aus?
Um die richtigen Farbstoffe und Additive für Spritzgussteile auszuwählen, muss man mehrere Faktoren berücksichtigen, wie z. B. die Art des Kunststoffs, die gewünschte Farbe und Funktion, die Kosten und die Umweltverträglichkeit. Die Art des Kunststoffs bestimmt, welche Farbstoffe und Additive kompatibel sind und wie sie sich auf die Eigenschaften des Materials auswirken. Die gewünschte Farbe und Funktion beeinflussen, welche Farbstoffe und Additive die ästhetischen und funktionalen Anforderungen erfüllen können. Die Kosten und die Umweltverträglichkeit hängen davon ab, wie viel Farbstoff oder Additiv benötigt wird, wie leicht es zu verarbeiten und zu entsorgen ist und ob es gesundheits- oder umweltschädlich ist. Um die optimale Auswahl zu treffen, sollte man sorgfältig die Vor- und Nachteile der verschiedenen Farbstoffe und Additive vergleichen und die spezifischen Bedürfnisse der Anwendung berücksichtigen.
Farbstoffe für Spritzguss
- Die verschiedenen Arten von Farbstoffen: Masterbatch, Flüssigfarbe, Pulver, Granulat
Es gibt verschiedene Arten von Farbstoffen, die für Spritzgussteile verwendet werden können, je nach den gewünschten Eigenschaften und Anforderungen. Die gängigsten sind Masterbatch, Flüssigfarbe, Pulver und Granulat. Masterbatch ist eine feste Mischung aus Farbstoff und Kunststoffträger, die in Form von Pellets oder Chips geliefert wird. Masterbatch bietet eine hohe Farbintensität, eine gleichmäßige Verteilung und eine einfache Handhabung, erfordert aber eine höhere Dosierung und kann die mechanischen Eigenschaften des Kunststoffs beeinträchtigen. Flüssigfarbe ist eine flüssige Mischung aus Farbstoff und Lösungsmittel, die direkt in den Schmelzestrom injiziert wird. Flüssigfarbe bietet eine niedrige Dosierung, eine schnelle Farbwechsel und eine hohe Umweltverträglichkeit, kann aber teurer sein und erfordert eine spezielle Ausrüstung. Pulver ist ein feines, trockenes Farbpigment, das mit dem Kunststoffgranulat vermischt oder auf die Oberfläche des fertigen Teils aufgetragen wird. Pulver bietet eine kostengünstige und flexible Lösung, kann aber eine ungleichmäßige Färbung, eine schlechte Haftung und eine hohe Staubentwicklung verursachen. Granulat ist ein vorgefärbtes Kunststoffmaterial, das direkt in den Spritzgussprozess eingebracht wird. Granulat bietet eine hohe Farbgenauigkeit, eine gute Beständigkeit und eine minimale Verschmutzung, kann aber die Auswahl an verfügbaren Farben einschränken und eine Lagerhaltung erfordern.
- Die Vor- und Nachteile der verschiedenen Farbstoffe
Die Wahl des Farbstoffs für Spritzgussteile hängt von mehreren Faktoren ab, wie z. B. dem Kunststofftyp, dem Produktionsvolumen, dem Design, dem Budget und den Umweltaspekten. Jede Art von Farbstoff hat ihre eigenen Vor- und Nachteile, die sorgfältig abgewogen werden müssen. Die folgende Tabelle zeigt einen Vergleich der wichtigsten Merkmale der vier Farbstoffarten:
Farbstoffart |
Farbintensität |
Farbverteilung |
Dosierung |
Farbwechsel |
Umweltverträglichkeit |
Kosten |
Mechanische Eigenschaften |
Masterbatch |
Hoch |
Gleichmäßig |
Hoch |
Mittel |
Mittel |
Günstig |
Verschlechtert |
Flüssigfarbe |
Mittel |
Gleichmäßig |
Niedrig |
Schnell |
Hoch |
Teuer |
Unverändert |
Pulver |
Mittel |
Ungleichmäßig |
Mittel |
Langsam |
Niedrig |
Günstig |
Unverändert |
Granulat |
Hoch |
Gleichmäßig |
Niedrig |
Langsam |
Hoch |
Teuer |
Unverändert |
Wie man aus der Tabelle ersehen kann, gibt es keinen idealen Farbstoff, der alle Kriterien erfüllt. Masterbatch ist die am häufigsten verwendete Farbstoffart, da sie eine hohe Farbqualität und eine einfache Handhabung bietet. Allerdings kann sie auch die mechanischen Eigenschaften des Kunststoffs negativ beeinflussen und eine höhere Dosierung erfordern, was zu mehr Abfall führen kann. Flüssigfarbe ist eine umweltfreundliche und effiziente Lösung, die eine niedrige Dosierung und einen schnellen Farbwechsel ermöglicht. Sie ist jedoch teurer als andere Farbstoffe und benötigt> eine spezielle Ausrüstung für die Lagerung und Dosierung. Pulver ist eine kostengünstige und flexible Lösung, die eine Vielzahl von Farbtönen erzeugen kann. Es kann jedoch auch zu einer ungleichmäßigen Färbung, einer schlechten Haftung und einer hohen Staubentwicklung führen, was die Qualität und Sicherheit der Produkte beeinträchtigt. Granulat ist eine hochwertige und beständige Lösung, die eine hohe Farbgenauigkeit und eine minimale Verschmutzung gewährleistet. Es ist jedoch auch die teuerste Farbstoffart und schränkt die Auswahl an verfügbaren Farben ein. Außerdem erfordert es eine Lagerhaltung, was zu mehr Platzbedarf und Logistikkosten führt.
Die Entscheidung für einen Farbstoff sollte daher auf einer sorgfältigen Analyse der spezifischen Anforderungen jedes Projekts basieren. Dabei sollte man die Vor- und Nachteile jeder Farbstoffart abwägen und die optimalste Lösung finden, die sowohl die technischen als auch die ästhetischen Aspekte berücksichtigt.
- Die wichtigsten Faktoren, die die Farbwirkung beeinflussen: Temperatur, Druck, Schmelzindex, Scherung, Form
Die Farbwirkung eines Kunststoffs hängt nicht nur von der Art des verwendeten Farbstoffs ab, sondern auch von verschiedenen Faktoren, die während des Spritzgussprozesses auftreten. Diese Faktoren können sowohl die physikalischen als auch die chemischen Eigenschaften des Kunststoffs und des Farbstoffs verändern und zu einer unerwünschten oder inkonsistenten Färbung führen. Die wichtigsten Faktoren, die die Farbwirkung beeinflussen, sind:
– Temperatur: Die Temperatur der Schmelze, des Werkzeugs und der Umgebung kann die Farbverteilung, die Klarheit, die Intensität und den Glanz des Kunststoffs beeinflussen. Eine zu hohe oder zu niedrige Temperatur kann zu einer Verfärbung, einer Trübung oder einer Versprödung des Kunststoffs führen. Die optimale Temperatur hängt vom Typ des Kunststoffs und des Farbstoffs ab und sollte sorgfältig eingestellt und kontrolliert werden.
– Druck: Der Druck, der auf die Schmelze ausgeübt wird, um sie in die Form zu injizieren, kann die Viskosität, die Kristallisation, die Schrumpfung und die Festigkeit des Kunststoffs beeinflussen. Ein zu hoher oder zu niedriger Druck kann zu einer ungleichmäßigen Färbung, einer Verformung oder einer Rissbildung des Kunststoffs führen. Der optimale Druck hängt vom Typ des Kunststoffs und des Farbstoffs ab und sollte sorgfältig eingestellt und kontrolliert werden.
– Schmelzindex: Der Schmelzindex ist ein Maß für die Fließfähigkeit der Schmelze bei einer bestimmten Temperatur und einem bestimmten Druck. Er beeinflusst die Füllung der Form, die Formbeständigkeit, die Schweißbarkeit und die Haltbarkeit des Kunststoffs. Ein hoher Schmelzindex bedeutet eine geringere Viskosität und eine bessere Fließfähigkeit, was zu einer besseren Färbung führen kann. Ein niedriger Schmelzindex bedeutet eine höhere Viskosität und eine schlechtere Fließfähigkeit, was zu einer schlechteren Färbung führen kann. Der optimale Schmelzindex hängt vom Typ des Kunststoffs und des Farbstoffs ab und sollte sorgfältig ausgewählt und überprüft werden.
– Scherung: Die Scherung ist die Verformung der Schmelze durch die angewandte Kraft, die zu einer Erhöhung der Temperatur und der Geschwindigkeit der Schmelze führt. Sie kann die Farbe, die H> eIligkeit, die Transparenz und die Glätte des Kunststoffs beeinflussen. Eine hohe Scherung kann zu einer Erhöhung der Farbintensität und des Glanzes führen, aber auch zu einer Verringerung der Klarheit und der Festigkeit. Eine niedrige Scherung kann zu einer Verringerung der Farbintensität und des Glanzes führen, aber auch zu einer Erhöhung der Klarheit und der Festigkeit. Die optimale Scherung hängt vom Typ des Kunststoffs und des Farbstoffs ab und sollte sorgfältig eingestellt und kontrolliert werden.
– Form: Die Form ist das Werkzeug, das die Schmelze in die gewünschte Form bringt. Sie beeinflusst die Füllung, die Abkühlung, die Entformung und die Oberfläche des Kunststoffs. Die Form sollte die richtige Größe, Form, Konstruktion, Material, Beschichtung, Temperatur, Druck und Zykluszeit haben, um eine gleichmäßige und qualitativ hochwertige Färbung zu gewährleisten. Die Form sollte auch regelmäßig gereinigt und gewartet werden, um Verunreinigungen, Verschleiß und Schäden zu vermeiden.
Diese Faktoren sind miteinander verbunden und beeinflussen sich gegenseitig. Daher ist es wichtig, ein gutes Verständnis für die Wechselwirkungen zwischen dem Kunststoff, dem Farbstoff und dem Spritzgussprozess zu haben, um die bestmögliche Farbwirkung zu erzielen.
- Die häufigsten Farbprobleme und wie man sie vermeidet: Verfärbung, Streifen, Flecken, Verblassen, Migration
– Verfärbung: Dies ist ein Problem, bei dem die Farbe des Kunststoffs nicht der gewünschten Farbe entspricht. Dies kann durch eine falsche Auswahl oder Dosierung des Farbstoffs, eine unzureichende Mischung oder Homogenisierung, eine ungleichmäßige Temperatur oder Druck in der Form, eine Kontamination durch Restmaterial oder andere Faktoren verursacht werden. Um Verfärbungen zu vermeiden, sollte man die Kompatibilität des Farbstoffs mit dem Kunststoff überprüfen, die richtige Menge an Farbstoff verwenden, die Schmelze gründlich mischen, die Formbedingungen kontrollieren und die Maschine und die Form sauber halten.
– Streifen: Dies sind sichtbare Linien oder Muster auf der Oberfläche des Kunststoffs, die durch eine inkonsistente Füllung oder Abkühlung, eine schlechte Fließeigenschaft der Schmelze, eine mangelnde Ventilation der Form, eine falsche Ausrichtung der Formhälften oder eine hohe Scherung verursacht werden. Um Streifen zu vermeiden, sollte man die Viskosität und die Temperatur der Schmelze anpassen, die Form so gestalten, dass sie eine gleichmäßige Füllung und Abkühlung ermöglicht, die Belüftung der Form verbessern, die Form richtig ausrichten und die Schergeschwindigkeit reduzieren.
– Flecken: Dies sind kleine Punkte oder Bereiche auf der Oberfläche des Kunststoffs, die sich in der Farbe oder im Glanz von der Umgebung unterscheiden. Sie können durch Verschmutzung, Blasenbildung, Verbrennung, Oxidation, Feuchtigkeit, Verkrustung oder andere Defekte im Kunststoff oder im Farbstoff verursacht werden. Um Flecken zu vermeiden, sollte man die Qualität des Kunststoffs und des Farbstoffs sicherstellen, die Feuchtigkeit im Material reduzieren, die Entgasung der Schmelze verbessern, die Temperatur und den Druck in der Form optimieren und die Form regelmäßig reinigen.
– Verblassen: Dies ist ein Problem, bei dem die Farbe des Kunststoffs mit der Zeit schwächer oder blasser wird. Dies kann durch eine unzureichende Konzentration oder Stabilität des Farbstoffs, eine hohe Temperatur oder UV-Strahlung, eine chemische Reaktion oder einen Abbau des Kunststoffs oder des Farbstoffs verursacht werden. Um das Verblassen zu vermeiden, sollte man einen hochwertigen und beständigen Farbstoff wählen, die Farbstoffmenge erhöhen, den Kunststoff vor Hitze und Licht schützen>
– Migration: Dies ist ein Problem, bei dem der Farbstoff aus dem Kunststoff austritt oder sich in andere Bereiche bewegt. Dies kann zu einer Veränderung oder einem Verlust der Farbe, einer Fleckenbildung oder einer Verschmutzung anderer Materialien führen. Dies kann durch eine geringe Affinität des Farbstoffs zum Kunststoff, eine hohe Mobilität oder Diffusivität des Farbstoffs, eine hohe Temperatur oder Druck, eine lange Lagerung oder einen Kontakt mit anderen Substanzen verursacht werden. Um die Migration zu vermeiden, sollte man einen geeigneten und festen Farbstoff für den Kunststoff auswählen, die Formbedingungen anpassen, den Kunststoff kühl und trocken lagern und den Kontakt mit anderen Materialien vermeiden.
Additive für Spritzguss
- Die verschiedenen Arten von Additiven: Stabilisatoren, Antioxidantien, Gleitmittel, Antistatika, Flammschutzmittel, UV-Schutzmittel, Biokompatibilitätsmittel, Verstärkungsmittel, Füllstoffe
Die verschiedenen Arten von Additiven für Spritzguss
Additive sind Zusatzstoffe, die dem Kunststoff zugesetzt werden, um seine Eigenschaften zu verbessern oder zu modifizieren. Sie können je nach ihrer Funktion und Wirkung in verschiedene Kategorien eingeteilt werden:
Stabilisatoren: Sie schützen den Kunststoff vor thermischer oder oxidativer Zersetzung während der Verarbeitung oder Lagerung. Sie verlängern die Lebensdauer des Kunststoffs und verhindern Verfärbungen oder Versprödung. Beispiele für Stabilisatoren sind Phenole, Phosphite, Thioester und Metalldesaktivatoren.
Antioxidantien: Sie sind eine spezielle Art von Stabilisatoren, die den Kunststoff vor dem Angriff von Sauerstoffradikalen schützen. Sie vermeiden Kettenabbrüche und Vernetzungen, die zu einer Verschlechterung der mechanischen Eigenschaften führen können. Beispiele für Antioxidantien sind Aminverbindungen, Hydrazide, Hydrochinone und Thioether.
Gleitmittel: Sie reduzieren die Reibung zwischen dem Kunststoff und der Form oder anderen Oberflächen. Sie erleichtern die Entformung, verbessern das Fließverhalten und die Oberflächenglattheit des Kunststoffs. Sie können intern oder extern wirken. Beispiele für Gleitmittel sind Wachse, Stearate, Silikone, Öle und Fette.
Antistatika: Sie verhindern die Ansammlung von statischer Elektrizität auf der Kunststoffoberfläche, die zu Staubanhaftung, Funkenbildung oder elektrischen Schlägen führen kann. Sie erhöhen die Leitfähigkeit oder die Dielektrizitätskonstante des Kunststoffs. Beispiele für Antistatika sind ionische Verbindungen, Feuchthaltemittel, Tenside und leitfähige Polymere.
Flammschutzmittel: Sie verringern die Entflammbarkeit oder die Ausbreitung von Flammen im Falle eines Brandes. Sie können durch physikalische oder chemische Mechanismen wirken, wie z. B. Abschirmung, Verdünnung, Kühlung oder Radikalfänger. Beispiele für Flammschutzmittel sind Halogenverbindungen, Stickstoffverbindungen, Phosphorverbindungen und anorganische Füllstoffe.
UV-Schutzmittel: Sie schüt>zen den Kunststoff vor der schädlichen Wirkung von ultraviolettem Licht, das zu einer photochemischen Zersetzung, Verfärbung oder Versprödung führen kann. Sie absorbieren oder reflektieren die UV-Strahlung oder bilden einen Schutzfilm auf der Kunststoffoberfläche. Beispiele für UV-Schutzmittel sind Benzophenone, Benzotriazole, Oxalanilide und anorganische Pigmente.
Biokompatibilitätsmittel: Sie verbessern die Verträglichkeit des Kunststoffs mit lebenden Geweben oder Organismen. Sie können die Bioabbaubarkeit, die Blutverträglichkeit, die Sterilisierbarkeit oder die Biostabilität des Kunststoffs erhöhen. Sie können auch antibakterielle, antimykotische oder antivirale Eigenschaften verleihen. Beispiele für Biokompatibilitätsmittel sind Polymilchsäure, Polyglykolsäure, Polyhydroxyalkanoate und Silbernanopartikel.
Verstärkungsmittel: Sie erhöhen die Zugfestigkeit, die Biegefestigkeit, die Steifigkeit oder die Schlagzähigkeit des Kunststoffs. Sie bestehen aus Fasern, Partikeln oder Plättchen, die eine höhere Festigkeit als der Kunststoff haben. Sie bilden eine Verbundstruktur mit dem Kunststoffmatrix. Beispiele für Verstärkungsmittel sind Glasfasern, Kohlenstofffasern, Keramikpartikel und Nanoröhren.
Füllstoffe: Sie verringern die Kosten, das Gewicht oder den Schrumpf des Kunststoffs. Sie bestehen aus pulverförmigen oder granularen Materialien, die den Kunststoff verdünnen oder verdicken. Sie können die Farbe, die Härte, die Wärmeleitfähigkeit oder die Dimensionsstabilität des Kunststoffs beeinflussen. Beispiele für Füllstoffe sind Kreide, Talkum, Kaolin und Holzmehl.
- Die Vor- und Nachteile der verschiedenen Additive
Die Vor- und Nachteile der verschiedenen Additive
Die Auswahl der geeigneten Additive für einen bestimmten Kunststoff hängt von den gewünschten Eigenschaften, den Kosten, der Verfügbarkeit und der Verarbeitbarkeit ab. Die Zugabe von Additiven kann sowohl positive als auch negative Auswirkungen auf das Endprodukt haben. Einige der möglichen Vorteile sind:
– Verbesserung der mechanischen, thermischen, elektrischen, optischen oder chemischen Eigenschaften des Kunststoffs
– Erhöhung der Funktionalität, Leistung oder Effizienz des Kunststoffs
– Erweiterung der Anwendungsmöglichkeiten oder des Marktanteils des Kunststoffs
– Reduzierung der Herstellungs- oder Betriebskosten des Kunststoffs
– Einführung neuer ästhetischer oder sensorischer Qualitäten des Kunststoffs
– Schutz des Kunststoffs vor Umwelteinflüssen oder Alterungsprozessen
Einige der möglichen Nachteile sind:
– Verschlechterung der mechanischen, thermischen, elektrischen, optischen oder chemischen Eigenschaften des Kunststoffs
– Verringerung der Funktionalität, Leistung oder Effizienz des Kunststoffs
– Einschränkung der Anwendungsmöglichkeiten oder des Marktanteils des Kunststoffs
– Erhöhung der Herstellungs- oder Betriebskosten des Kunststoffs
– Verlust der ästhetischen oder sensorischen Qualitäten des Kunststoffs
– Schädigung des Kunststoffs durch unerwünschte Reaktionen oder Nebenprodukte
Daher ist es wichtig, die Vor- und Nachteile der verschiedenen Additive sorgfältig abzuwägen und die optimale Formulierung für jeden spezifischen Zweck zu finden. Die Additivtechnologie ist ein dynamisches und innovatives Gebiet, das ständig neue Möglichkeiten und Herausforderungen bietet.
- Die wichtigsten Faktoren, die die Additivwirkung beeinflussen: Dosierung, Kompatibilität, Verteilung, Wechselwirkung, Alterung
Die wichtigsten Faktoren, die die Additivwirkung beeinflussen: Dosierung, Kompatibilität, Verteilung, Wechselwirkung, Alterung
Die Wirkung eines Additivs hängt von verschiedenen Faktoren ab, die berücksichtigt werden müssen, um die gewünschten Ergebnisse zu erzielen. Diese sind:
– Dosierung: Die Menge des Additivs, die dem Kunststoff zugesetzt wird, bestimmt seine Effizienz und seine Kosten-Nutzen-Relation. Zu wenig Additiv kann die erforderliche Funktion nicht erfüllen, während zu viel Additiv zu Verschwendung, Überdosierung oder negativen Nebeneffekten führen kann. Die optimale Dosierung hängt von der Art des Additivs, der Art des Kunststoffs, dem Verarbeitungsverfahren und der Endanwendung ab.
– Kompatibilität: Die Kompatibilität bezieht sich auf die Fähigkeit des Additivs, sich gleichmäßig mit dem Polymer zu mischen, ohne dessen Eigenschaften zu beeinträchtigen oder unerwünschte Phasentrennung oder Ausblutung zu verursachen. Die Kompatibilität hängt von der chemischen Struktur, der Polarität, der Molekülgröße und der Kristallinität des Additivs und des Kunststoffs ab. Inkompatible Additive können zu einer verringerten Wirksamkeit, einer Verschlechterung der mechanischen Eigenschaften oder einer Beeinträchtigung der Ästhetik führen.
– Verteilung: Die Verteilung bezieht sich auf die Gleichmäßigkeit, mit der das Additiv im Kunststoff verteilt ist. Eine gute Verteilung ermöglicht eine homogene Wirkung des Additivs im gesamten Material, während eine schlechte Verteilung zu lokalen Konzentrationsunterschieden, Agglomerationen oder Klumpen führen kann. Die Verteilung hängt von der Verarbeitungstemperatur, der Schmelzviskosität, der Scherrate, dem Mischverfahren und dem Dispergiervermögen des Additivs ab. Eine schlechte Verteilung kann zu einer reduzierten Wirksamkeit, einer ungleichmäßigen Farbe, einer verringertern Transparenz oder einer geringeren Beständigkeit führen.
– Wechselwirkung: Die Wechselwirkung bezieht sich auf die möglichen chemischen oder physikalischen Interaktionen zwischen dem Additiv und dem Kunststoff oder anderen Additiven. Solche Interaktionen können die Wirkung des Additivs verstärken, abschwächen oder verändern,> und können sowohl positive als auch negative Auswirkungen haben. Die Wechselwirkung hängt von der Reaktivität, der Affinität, der Polarität und der Stabilität des Additivs und des Kunststoffs ab. Mögliche Wechselwirkungen sind zum Beispiel Katalyse, Antagonismus, Synergismus oder Komplexierung.
– Alterung: Die Alterung bezieht sich auf die Veränderung des Additivs oder des Kunststoffs im Laufe der Zeit unter dem Einfluss von externen Faktoren wie Licht, Wärme, Feuchtigkeit, Sauerstoff, Mikroorganismen oder mechanischem Stress. Die Alterung kann zu einer Abnahme oder einem Verlust der Additivwirkung, einer Freisetzung von flüchtigen Substanzen, einer Verfärbung, einer Sprödheit oder einer Rissbildung führen. Die Alterung hängt von der Art, der Qualität, der Stabilität und der Menge des Additivs und des Kunststoffs sowie von den Lagerbedingungen ab.
Diese Faktoren sind eng miteinander verbunden und beeinflussen sich gegenseitig, so dass eine systematische und ganzheitliche Betrachtungsweise notwendig ist, um die optimale Additivwirkung zu erreichen.
- Die häufigsten Additivprobleme und wie man sie vermeidet: Verlust der mechanischen Eigenschaften, Veränderung der Oberflächenqualität, Geruch, Geschmack, Toxizität, Umweltverträglichkeit
Die häufigsten Additivprobleme und wie man sie vermeidet: Verlust der mechanischen Eigenschaften, Veränderung der Oberflächenqualität, Geruch, Geschmack, Toxizität, Umweltverträglichkeit
Einige der häufigsten Additivprobleme, die bei der Herstellung und Verwendung von Kunststoffen auftreten können, sind:
– Verlust der mechanischen Eigenschaften: Dies kann durch den Abbau des Additivs oder des Kunststoffs selbst verursacht werden, z. B. durch Oxidation, Hydrolyse, Thermische Alterung oder Fotooxidation. Um dies zu vermeiden, sollten stabile, hochwertige und geeignete Additive ausgewählt werden, die mit dem Kunststoff kompatibel sind und dessen Leistung verbessern. Außerdem sollten die optimale Dosierung, die richtige Verarbeitungstemperatur und die angemessene Lagerung beachtet werden.
– Veränderung der Oberflächenqualität: Dies kann sich als Verfärbung, Fleckenbildung, Glanzverlust, Kratzer oder Abrieb äußern. Die Ursachen können vielfältig sein, wie z. B. eine ungleichmäßige Verteilung des Additivs im Kunststoff, eine Wechselwirkung zwischen dem Additiv und dem Kunststoff oder anderen Bestandteilen, eine unzureichende Reinigung der Form oder eine Verschmutzung durch Fremdstoffe. Um dies zu vermeiden, sollten homogene, farbechte und beständige Additive verwendet werden, die die gewünschten optischen Effekte erzielen, ohne die Oberfläche zu beeinträchtigen. Außerdem sollten die richtige Mischung, die korrekte Spritzgusstechnik und die regelmäßige Wartung der Form sichergestellt werden.
– Geruch, Geschmack, Toxizität: Diese Probleme können auftreten, wenn das Additiv oder der Kunststoff flüchtige organische Verbindungen (VOCs), Schwermetalle, endokrine Disruptoren oder andere schädliche Substanzen freisetzen, die die Gesundheit oder die Sicherheit der Nutzer gefährden können. Dies gilt insbesondere für Anwendungen, die mit Lebensmitteln oder der Haut in Kontakt kommen, wie z. B. Verpackungen, Spielzeug oder Kosmetika. Um dies zu vermeiden, sollten unschädliche, geruchsarme und geschmacksneutrale Additive verwendet werden, die den geltenden gesetzlichen Vorschriften und Normen entsprechen. Außerdem sollten die erforderlichen Tests und Zertifikate durchgeführt und eingeholt werden, um die Qualität und die Unbedenklichkeit> des Endprodukts zu gewährleisten.
– Umweltverträglichkeit: Dieses Problem bezieht sich auf die Auswirkungen des Additivs oder des Kunststoffs auf die Umwelt, wie z. B. die Abbaubarkeit, die Kompostierbarkeit, die Recyclingfähigkeit oder die CO2-Bilanz. Da die Nachfrage nach nachhaltigen Kunststofflösungen immer größer wird, sollten die Additive die ökologischen Eigenschaften des Kunststoffs verbessern oder zumindest nicht verschlechtern. Um dies zu erreichen, sollten biobasierte, biologisch abbaubare oder recycelte Additive bevorzugt werden, die die Ressourceneffizienz erhöhen und den Abfall reduzieren. Außerdem sollten die potenziellen Umweltauswirkungen des Additivs oder des Kunststoffs entlang des gesamten Lebenszyklus bewertet werden.
Fazit
- Zusammenfassung der wichtigsten Erkenntnisse und Empfehlungen
In diesem Bericht haben wir die wichtigsten Aspekte der Farbstoffe und Additive für Spritzguss untersucht, wie z. B. ihre Funktionen, Anwendungen, Herausforderungen und Möglichkeiten. Wir haben einige Beispiele für innovative Additive vorgestellt, die die Leistung, das Erscheinungsbild oder die Umweltverträglichkeit von Kunststoffen verbessern können. Wir empfehlen den Herstellern, sich über die neuesten Entwicklungen im Bereich der Farbstoffe und Additive auf dem Laufenden zu halten und die Anforderungen ihrer Kunden und Märkte zu berücksichtigen. Außerdem sollten sie die gesetzlichen Vorschriften und Normen einhalten, die die Verwendung von bestimmten Additiven einschränken oder regeln können. Schließlich sollten sie die potenziellen Vorteile und Risiken jeder Additivlösung sorgfältig abwägen und ihre Auswirkungen auf die Qualität, Sicherheit und Nachhaltigkeit des Endprodukts bewerten. Wenn Sie mehr über die Farbstoffe und Additive für Spritzguss erfahren möchten, kontaktieren Sie uns bitte unter [EMAIL] oder besuchen Sie unsere Website [URL].
- Ausblick auf zukünftige Trends und Entwicklungen im Bereich der Farbstoffe und Additive für Spritzguss
Der Markt für Farbstoffe und Additive für Spritzguss ist ständig in Bewegung und bietet neue Möglichkeiten für Innovation und Differenzierung. Einige der wichtigsten Trends und Entwicklungen, die in den nächsten Jahren zu beobachten sind, sind:
– Die steigende Nachfrage nach biobasierten, biologisch abbaubaren oder recycelbaren Kunststoffen, die eine geringere Umweltbelastung verursachen und den Verbrauchererwartungen entsprechen. Dies erfordert die Entwicklung von kompatiblen und leistungsfähigen Farbstoffen und Additiven, die die Eigenschaften dieser Materialien verbessern oder erhalten können.
– Die zunehmende Digitalisierung und Personalisierung der Fertigung, die eine höhere Flexibilität und Anpassbarkeit der Kunststoffprodukte ermöglicht. Dies eröffnet neue Möglichkeiten für intelligente, interaktive oder funktionale Farbstoffe und Additive, die auf Stimuli wie Temperatur, Licht, Feuchtigkeit oder elektrische Signale reagieren können.
– Die wachsenden Herausforderungen im Zusammenhang mit der Qualitätssicherung, der Rückverfolgbarkeit und dem Schutz der Kunststoffprodukte vor Fälschung, Manipulation oder Diebstahl. Dies erfordert die Entwicklung von speziellen Farbstoffen und Additiven, die als Markierungs-, Identifikations- oder Sicherheitsmittel dienen können, z. B. fluoreszierende, thermochrome, magnetische oder RFID-basierte Lösungen.
Diese Trends und Entwicklungen bieten spannende Möglichkeiten für die Hersteller von Farbstoffen und Additiven für Spritzguss, erfordern aber auch eine kontinuierliche Forschung und Entwicklung, um die Leistung, die Kosten und die regulatorische Konformität ihrer Produkte zu gewährleisten. Wir bei [FIRMA] haben das Know-how, die Erfahrung und die Ressourcen, um Sie bei der Auswahl und Anwendung der besten Farbstoff- und Additivlösungen für Ihre Spritzgussanwendungen zu unterstützen.
- Aufforderung zum Handeln und Kontaktmöglichkeit
Wenn Sie mehr über unsere innovativen Farbstoff- und Additivlösungen für Spritzguss erfahren möchten, zögern Sie nicht, uns zu kontaktieren. Wir beraten Sie gerne persönlich und erstellen Ihnen ein individuelles Angebot, das Ihren Anforderungen entspricht. Sie können uns telefonisch, per E-Mail oder über unser Online-Kontaktformular erreichen. Wir freuen uns auf Ihre Anfrage und darauf, mit Ihnen zusammenzuarbeiten.