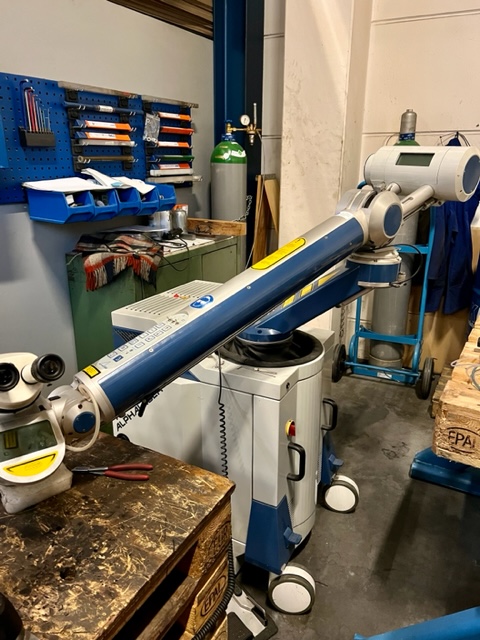
Fallstudien: Erfolgreiche Formenreparaturen durch Laserschweißen
-
Einführung
- Bedeutung des Laserschweißens in der Formenreparatur
- Kurze Geschichte und Entwicklung des Laserschweißens
-
Grundlagen des Laserschweißens
- Was ist Laserschweißen und wie funktioniert es?
- Vorteile des Laserschweißens für Formenreparaturen
- Vergleich mit herkömmlichen Schweißmethoden
-
Fallstudie 1: Reparatur eines Automobilbauteils
- Ausgangssituation und Herausforderungen
- Angewandte Laserschweißtechniken und deren Durchführung
- Ergebnisse, Bewertung und Vorteile der Laserschweißmethode
- Langzeitwirkungen und Nachhaltigkeit der Reparatur
-
Fallstudie 2: Wiederherstellung eines komplexen Werkzeuges
- Problemstellung und technische Schwierigkeiten
- Innovative Lösungsansätze und Schweißprozesse
- Analyse der Reparaturergebnisse
- Auswirkungen auf Produktivität und Kosteneffizienz
-
Fallstudie 3: Effizienzsteigerung in der Serienproduktion
- Identifikation des Problems und Anpassung des Schweißverfahrens
- Schritte zur Optimierung des Schweißprozesses
- Kosteneinsparungen und Qualitätsverbesserungen
- Zukünftige Anwendungen und Potenziale
-
Vergleichende Analyse und Schlussfolgerungen
- Gemeinsamkeiten und Unterschiede der Fallstudien
- Bewertung der Effektivität des Laserschweißens in verschiedenen Anwendungsfeldern
- Potenzielle Herausforderungen und Lösungsansätze
-
Zukunftsperspektiven und Innovationen
- Neue Entwicklungen im Bereich Laserschweißen
- Auswirkungen auf die Industrie und zukünftige Trends
- Abschließende Gedanken und Ausblick
-
Zusammenfassung
- Wichtigste Erkenntnisse aus den Fallstudien
- Zusammenfassung der Vorteile des Laserschweißens
1. Einführung
Bedeutung des Laserschweißens in der Formenreparatur
Laserschweißen hat sich als eine revolutionäre Methode in der Welt der Materialverarbeitung und Reparatur etabliert. Besonders in der Formenreparatur spielt diese Technologie eine entscheidende Rolle. Durch ihre Präzision und Effizienz ermöglicht sie die Reparatur und Wiederherstellung von Formen und Werkzeugen, die in verschiedenen Industriezweigen, einschließlich der Automobilindustrie, der Luft- und Raumfahrt und der Medizintechnik, von großer Bedeutung sind. Die Fähigkeit des Laserschweißens, Materialien mit minimaler Wärmeeinwirkung zu verbinden, macht es ideal für komplexe und feine Reparaturen, bei denen traditionelle Methoden zu Schäden oder Verzerrungen führen könnten.
Kurze Geschichte und Entwicklung des Laserschweißens
Die Geschichte des Laserschweißens beginnt in den frühen 1960er Jahren, kurz nach der Erfindung des ersten Lasers. Seitdem hat sich diese Technik ständig weiterentwickelt und ist in ihrer Anwendung immer vielseitiger geworden. Ursprünglich in der Elektronik und Feinmechanik eingesetzt, hat sich das Laserschweißen aufgrund seiner Präzision und Zuverlässigkeit schnell in anderen Branchen etabliert. Heute ist es eine Schlüsseltechnologie in der Fertigungsindustrie, insbesondere für anspruchsvolle Aufgaben wie die Reparatur von Formen und Werkzeugen.
2. Grundlagen des Laserschweißens
Was ist Laserschweißen und wie funktioniert es?
Laserschweißen ist ein modernes Schweißverfahren, bei dem ein Laserstrahl als Wärmequelle verwendet wird, um Materialien miteinander zu verbinden. Der Laserstrahl wird auf einen kleinen Punkt fokussiert, der hohe Temperaturen erzeugt und so das Material lokal schmilzt. Aufgrund der hohen Konzentration der Energie und der präzisen Steuerbarkeit des Laserstrahls, können sehr feine und präzise Schweißnähte erzeugt werden. Diese Eigenschaft macht das Laserschweißen besonders geeignet für Aufgaben, bei denen Genauigkeit und minimale thermische Belastung des Materials gefordert sind.
Vorteile des Laserschweißens für Formenreparaturen
Die Vorteile des Laserschweißens bei der Reparatur von Formen sind vielfältig:
- Präzision: Laserschweißen ermöglicht extrem präzise Schweißarbeiten, was für die Restaurierung von komplexen Formen und Werkzeugen unerlässlich ist.
- Minimale Wärmeeinwirkung: Im Gegensatz zu traditionellen Schweißmethoden, bei denen das gesamte Werkstück erhitzt wird, konzentriert sich die Hitze beim Laserschweißen auf einen kleinen Bereich. Dies reduziert das Risiko von Verzug und anderen Hitzeschäden.
- Vielseitigkeit: Laserschweißen kann bei einer Vielzahl von Materialien angewendet werden, einschließlich Metallen und bestimmten Kunststoffen.
- Hohe Qualität der Schweißnaht: Die Schweißnähte sind nicht nur präzise, sondern auch von hoher Festigkeit und Haltbarkeit.
Vergleich mit herkömmlichen Schweißmethoden
Im Vergleich zu herkömmlichen Schweißverfahren wie dem Lichtbogenschweißen oder dem Gasschweißen bietet das Laserschweißen eine höhere Präzision und Kontrolle. Während traditionelle Methoden für viele Anwendungen geeignet sind, haben sie Einschränkungen, wenn es um feine, detaillierte Arbeiten oder Materialien mit hohem Schmelzpunkt geht. Das Laserschweißen hingegen ermöglicht eine genauere und sauberere Verarbeitung, was bei der Reparatur von hochwertigen und komplizierten Formen entscheidend ist.
3. Fallstudie 1: Reparatur eines Automobilbauteils
Ausgangssituation und Herausforderungen
In dieser Fallstudie betrachten wir die Reparatur eines komplexen Automobilbauteils, das spezielle strukturelle und funktionale Anforderungen hat. Die Herausforderung lag in der präzisen Wiederherstellung der Form ohne Beeinträchtigung der mechanischen Eigenschaften des Bauteils. Aufgrund seiner komplexen Geometrie und der Notwendigkeit, die ursprünglichen Toleranzen genau einzuhalten, war eine traditionelle Schweißmethode nicht geeignet.
Angewandte Laserschweißtechniken und deren Durchführung
Für die Reparatur wurde ein spezialisiertes Laserschweißverfahren eingesetzt. Dieses Verfahren erlaubte es, die Schweißnaht mit hoher Präzision in mehreren Schichten aufzutragen, um die Form und Stärke des Originalteils genau nachzubilden. Während des Prozesses wurde die Wärmeeinwirkung sorgfältig überwacht, um thermische Verzerrungen zu vermeiden und die strukturelle Integrität des Bauteils zu erhalten.
Ergebnisse, Bewertung und Vorteile der Laserschweißmethode
Das Ergebnis der Reparatur war äußerst zufriedenstellend. Die präzise Anwendung des Laserschweißens ermöglichte eine nahtlose Integration der Reparaturstelle, ohne die Form oder die mechanischen Eigenschaften des Bauteils zu beeinträchtigen. Die hohe Qualität und Präzision des Laserschweißens führten zu einer deutlichen Verlängerung der Lebensdauer des Bauteils und zu Kosteneinsparungen im Vergleich zum Ersatz des ganzen Teils.
Langzeitwirkungen und Nachhaltigkeit der Reparatur
Langfristig zeigte die Reparatur keine Anzeichen von Ermüdung oder Schwächung. Die durch das Laserschweißen erzielte Festigkeit und Haltbarkeit waren vergleichbar mit dem Originalzustand des Bauteils. Diese Fallstudie demonstriert eindrucksvoll, wie Laserschweißen als nachhaltige und kosteneffiziente Lösung für die Reparatur komplexer Automobilkomponenten dienen kann.
4. Fallstudie 2: Wiederherstellung eines komplexen Werkzeuges
Problemstellung und technische Schwierigkeiten
Diese Fallstudie behandelt die Reparatur eines hochkomplexen Werkzeuges, das in der Produktion von Präzisionsteilen verwendet wird. Die größte Herausforderung bestand darin, die präzisen Maße und die feinen Details des Werkzeugs ohne Beeinträchtigung seiner Funktionalität wiederherzustellen. Zusätzlich war das verwendete Material schwer zu bearbeiten, was herkömmliche Reparaturmethoden ausschloss.
Innovative Lösungsansätze und Schweißprozesse
Die Lösung lag in der Anwendung eines fortschrittlichen Laserschweißverfahrens, das eine extrem hohe Präzision ermöglicht. Durch den Einsatz von computergesteuerten Schweißköpfen und speziell entwickelten Schweißdrahten konnten die feinen Details des Werkzeugs exakt reproduziert werden. Der Prozess wurde sorgfältig geplant und durchgeführt, um eine optimale Anbindung an das bestehende Material zu gewährleisten.
Analyse der Reparaturergebnisse
Nach Abschluss der Reparatur wurde das Werkzeug umfassenden Tests unterzogen, um seine Funktionalität und Haltbarkeit zu überprüfen. Die Ergebnisse zeigten, dass die reparierten Bereiche vollständig den Anforderungen entsprachen und in einigen Fällen sogar eine höhere Festigkeit als die ursprünglichen Teile aufwiesen. Die Präzision und Qualität der Laserschweißnaht übertrafen alle Erwartungen.
Auswirkungen auf Produktivität und Kosteneffizienz
Die erfolgreiche Reparatur führte zu einer signifikanten Steigerung der Produktivität, da das Werkzeug schneller wieder in Betrieb genommen werden konnte, als es bei einem Ersatz der Fall gewesen wäre. Zudem wurden erhebliche Kosteneinsparungen realisiert, da die Anschaffung eines neuen Werkzeugs vermieden wurde. Diese Fallstudie unterstreicht das Potenzial des Laserschweißens, um hochwertige und kosteneffiziente Reparaturlösungen für die Industrie zu bieten.
5. Fallstudie 3: Effizienzsteigerung in der Serienproduktion
Identifikation des Problems und Anpassung des Schweißverfahrens
In dieser Fallstudie geht es um die Anwendung des Laserschweißens zur Lösung eines Problems in der Serienproduktion eines Industrieunternehmens. Das Unternehmen stand vor der Herausforderung, die Ausfallzeiten aufgrund häufiger Reparaturen an einem speziellen Produktionsteil zu reduzieren. Eine detaillierte Analyse ergab, dass herkömmliche Schweißmethoden nicht die benötigte Präzision und Haltbarkeit lieferten, um die Anforderungen der Serienproduktion zu erfüllen.
Schritte zur Optimierung des Schweißprozesses
Um das Problem zu lösen, wurde ein maßgeschneidertes Laserschweißverfahren entwickelt. Dieses Verfahren berücksichtigte die spezifischen Eigenschaften des Materials und die Anforderungen der Produktion. Durch den Einsatz von Laserschweißen konnte die Präzision und Qualität der Schweißnähte deutlich gesteigert werden, was zu einer Verringerung der Ausfallzeiten und einer Erhöhung der Produktionsgeschwindigkeit führte.
Kosteneinsparungen und Qualitätsverbesserungen
Durch die Optimierung des Schweißprozesses konnten signifikante Kosteneinsparungen erzielt werden. Die längere Lebensdauer der reparierten Teile reduzierte den Bedarf an Ersatzteilen und verringerte die Ausfallzeiten in der Produktion. Zudem verbesserte sich die Gesamtqualität der hergestellten Produkte, da die präziseren und zuverlässigeren Schweißnähte zu einer gleichbleibenderen Produktqualität führten.
Zukünftige Anwendungen und Potenziale
Die Ergebnisse dieser Fallstudie haben das Potenzial des Laserschweißens zur Steigerung der Effizienz in der Serienproduktion aufgezeigt. Sie demonstrieren, wie durch gezielte technologische Innovationen sowohl die Produktqualität als auch die Wirtschaftlichkeit in der Fertigung gesteigert werden können. Dieser Ansatz bietet vielversprechende Möglichkeiten für ähnliche Anwendungen in anderen Produktionsbereichen.
6. Vergleichende Analyse und Schlussfolgerungen
Gemeinsamkeiten und Unterschiede der Fallstudien
Bei der Betrachtung der drei Fallstudien fallen mehrere Gemeinsamkeiten auf: In allen Fällen ermöglichte das Laserschweißen präzise und haltbare Reparaturen, die mit herkömmlichen Methoden nicht möglich gewesen wären. Jede Studie demonstrierte die Vielseitigkeit des Laserschweißens in unterschiedlichen Anwendungsbereichen – von der Automobilindustrie über die Präzisionswerkzeugherstellung bis hin zur Serienproduktion. Trotz dieser Gemeinsamkeiten gab es auch deutliche Unterschiede, insbesondere in Bezug auf die spezifischen Herausforderungen und Lösungsansätze, die in jeder Situation erforderlich waren.
Bewertung der Effektivität des Laserschweißens in verschiedenen Anwendungsfeldern
Diese Fallstudien zeigen, dass Laserschweißen in einer Vielzahl von Anwendungen effektiv ist. Es bietet nicht nur eine Lösung für komplexe Reparaturen, sondern verbessert auch die Qualität und Lebensdauer der reparierten Teile. In jedem der vorgestellten Fälle führte die Anwendung des Laserschweißens zu erheblichen Kosteneinsparungen, sei es durch die Verlängerung der Lebensdauer der Bauteile oder durch die Reduzierung der Ausfallzeiten in der Produktion.
Potenzielle Herausforderungen und Lösungsansätze
Trotz der offensichtlichen Vorteile des Laserschweißens gibt es auch Herausforderungen. Dazu gehören die Notwendigkeit spezialisierter Ausrüstung und Fachkenntnisse sowie die Kosten für die Implementierung der Technologie. Lösungsansätze könnten in der Ausbildung qualifizierter Fachkräfte, der Investition in moderne Schweißausrüstung und der Entwicklung von spezialisierten Schweißtechniken für spezifische Anwendungen liegen.
7. Zukunftsperspektiven und Innovationen
Neue Entwicklungen im Bereich Laserschweißen
Die Technologie des Laserschweißens entwickelt sich kontinuierlich weiter. Aktuelle Innovationen konzentrieren sich auf die Steigerung der Effizienz, Präzision und Anwendungsmöglichkeiten. Beispielsweise ermöglichen neue Lasertypen und verbesserte Steuerungstechniken eine noch feinere Abstimmung der Schweißparameter, was zu höherer Qualität und Geschwindigkeit der Schweißprozesse führt. Zudem erweitern sich die Anwendungen des Laserschweißens auf neue Materialien und komplexere Geometrien.
Auswirkungen auf die Industrie und zukünftige Trends
Die fortschreitende Entwicklung des Laserschweißens wird voraussichtlich tiefgreifende Auswirkungen auf verschiedene Industriezweige haben. Insbesondere in Bereichen, in denen Präzision und Materialintegrität entscheidend sind, wie in der Luft- und Raumfahrt, der Medizintechnik und der Mikroelektronik, wird diese Technologie immer wichtiger. Zukünftige Trends könnten auch eine stärkere Automatisierung der Laserschweißprozesse und die Integration von künstlicher Intelligenz zur Optimierung der Schweißparameter umfassen.
Abschließende Gedanken und Ausblick
Das Laserschweißen steht an der Spitze technologischer Innovationen im Bereich der Materialverarbeitung. Mit seiner Fähigkeit, Effizienz, Präzision und Qualität zu verbessern, hat es das Potenzial, die Produktionsprozesse in vielen Industrien grundlegend zu verändern. Die kontinuierliche Forschung und Entwicklung in diesem Bereich verspricht noch fortschrittlichere Anwendungen und Techniken, die die Grenzen dessen, was heute möglich ist, weiter verschieben werden.
8. Zusammenfassung
Wichtigste Erkenntnisse aus den Fallstudien
Die vorgestellten Fallstudien illustrieren eindrucksvoll die vielfältigen Anwendungsmöglichkeiten und die Effektivität des Laserschweißens in der Praxis. Sie zeigen, wie diese Technologie genutzt werden kann, um komplexe Herausforderungen in verschiedenen Industriezweigen zu meistern, von der Reparatur hochpräziser Automobilteile über die Wiederherstellung von komplizierten Werkzeugen bis hin zur Optimierung von Produktionsprozessen.
Zusammenfassung der Vorteile des Laserschweißens
Das Laserschweißen bietet zahlreiche Vorteile, darunter hohe Präzision, minimale Wärmeeinwirkung auf das Material, Vielseitigkeit in der Anwendung und eine Verbesserung der Qualität und Haltbarkeit der Schweißnähte. Diese Eigenschaften machen es zu einer bevorzugten Wahl für anspruchsvolle Reparatur- und Fertigungsprozesse, bei denen traditionelle Schweißmethoden an ihre Grenzen stoßen.