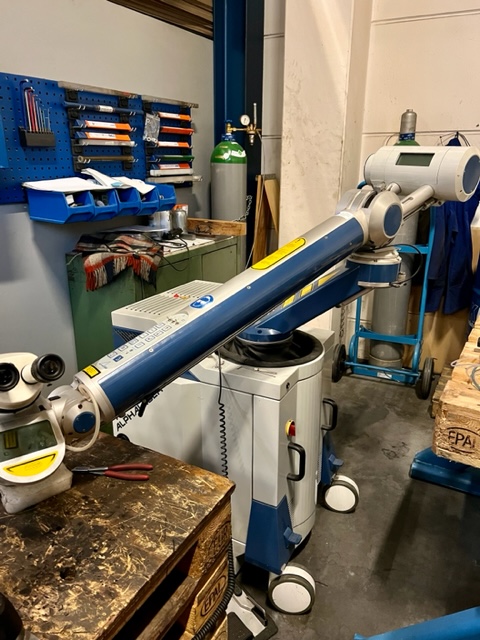
Ausbildung und Qualifikationen für das Laserschweißen zur Formenreparatur
Ausbildung und Qualifikationen für das Laserschweißen zur Formenreparatur
Ein Blogartikel von Intelligent Writing Assistant
- Was ist Laserschweißen und wie wird es zur Formenreparatur eingesetzt?
Inhaltsverzeichnis
- Welche Vorteile hat das Laserschweißen gegenüber anderen Schweißverfahren?
- Welche Anforderungen muss man erfüllen, um Laserschweißer zu werden?
- Welche Ausbildungsmöglichkeiten gibt es für das Laserschweißen?
- Welche Qualifikationen und Zertifikate sind für das Laserschweißen erforderlich?
- Wie sieht die Zukunft des Laserschweißens aus?
Was ist Laserschweißen und wie wird es zur Formenreparatur eingesetzt?
Laserschweißen ist ein Schweißverfahren, bei dem ein gebündelter Laserstrahl hoher Intensität genutzt wird, um Metalle oder andere Materialien miteinander zu verbinden. Das Laserschweißen zeichnet sich durch eine hohe Präzision, Geschwindigkeit und Qualität aus, die es für viele industrielle Anwendungen geeignet machen. Eine davon ist die Formenreparatur, bei der beschädigte oder verschlissene Formen, die zum Beispiel für die Kunststoff- oder Metallverarbeitung verwendet werden, mit Laserschweißen wiederhergestellt werden können. Dabei wird das defekte Material mit einem geeigneten Füllmaterial aufgefüllt, das mit dem Laserstrahl verschmolzen wird. Das Laserschweißen ermöglicht es, die Formen ohne große Wärmeeinflusszone oder Verzug zu reparieren, was die Lebensdauer und die Qualität der Formen erhöht.
Welche Vorteile hat das Laserschweißen gegenüber anderen Schweißverfahren?
Das Laserschweißen bietet im Vergleich zu anderen Schweißverfahren wie dem Lichtbogenschweißen, dem Widerstandsschweißen oder dem Ultraschallschweißen mehrere Vorteile, die es für die Formenreparatur attraktiv machen. Einige davon sind:
- Das Laserschweißen erzeugt eine sehr schmale und tiefe Schweißnaht, die eine hohe Festigkeit und Dichtigkeit aufweist.
- Das Laserschweißen erfordert keine zusätzlichen Schweißzusätze wie Elektroden oder Schutzgase, was die Kosten und die Umweltbelastung reduziert.
- Das Laserschweißen kann auch schwer zugängliche oder komplexe Formen schweißen, die mit anderen Verfahren nicht möglich sind.
- Das Laserschweißen kann verschiedene Materialien und Legierungen schweißen, die mit anderen Verfahren nicht kompatibel sind.
- Das Laserschweißen ist ein berührungsloses Verfahren, das die Verschleiß- und Wartungskosten minimiert.
Welche Anforderungen muss man erfüllen, um Laserschweißer zu werden?
Um Laserschweißer zu werden, muss man über einige grundlegende Fähigkeiten und Kenntnisse verfügen, die für die sichere und effiziente Durchführung des Verfahrens erforderlich sind. Dazu gehören:
- Ein gutes technisches Verständnis und eine hohe Konzentrationsfähigkeit.
- Ein gutes räumliches Vorstellungsvermögen und eine gute Hand-Augen-Koordination.
- Ein gutes Gefühl für die richtige Einstellung und Handhabung des Lasers und des Werkstücks.
- Ein gutes Wissen über die physikalischen und chemischen Eigenschaften der zu schweißenden Materialien und die möglichen Risiken und Nebenwirkungen des Lasers.
- Ein gutes Wissen über die geltenden Sicherheits- und Qualitätsstandards und die entsprechenden Schutzmaßnahmen.
Welche Ausbildungsmöglichkeiten gibt es für das Laserschweißen?
Es gibt verschiedene Möglichkeiten, sich für das Laserschweißen ausbilden zu lassen, je nach dem gewünschten Qualifikationsniveau und dem beruflichen Ziel. Einige davon sind:
- Eine Ausbildung zum Laserschweißer, die in der Regel zwei bis drei Jahre dauert und in Betrieben oder Berufsschulen angeboten wird. Dabei lernt man die theoretischen und praktischen Grundlagen des Laserschweißens und anderer Schweißverfahren, sowie die relevanten Fachkenntnisse in Mathematik, Physik, Werkstoffkunde, Technik und Sicherheit.
- Eine Weiterbildung zum Laserschweißfachmann, die in der Regel ein bis zwei Jahre dauert und in Fachschulen oder Akademien angeboten wird. Dabei vertieft man seine Kenntnisse und Fertigkeiten im Laserschweißen und erlernt zusätzliche Kompetenzen in der Planung, Steuerung, Überwachung und Optimierung von Schweißprozessen und -projekten.
- Ein Studium zum Laserschweißingenieur, das in der Regel drei bis vier Jahre dauert und an Hochschulen oder Universitäten angeboten wird. Dabei erwirbt man ein umfassendes Wissen und Verständnis für die physikalischen und technischen Grundlagen, die Anwendungen und die Innovationen des Laserschweißens und anderer Lasertechnologien, sowie die Fähigkeit, wissenschaftliche Methoden und Forschung anzuwenden.
Welche Qualifikationen und Zertifikate sind für das Laserschweißen erforderlich?
Um als Laserschweißer tätig zu werden, muss man in der Regel eine abgeschlossene Ausbildung oder Weiterbildung im Bereich des Laserschweißens oder einer verwandten Fachrichtung nachweisen können. Darüber hinaus muss man in der Regel auch eine gültige Schweißerprüfung oder ein anerkanntes Zertifikat besitzen, das die Befähigung und die Erfahrung im Laserschweißen bestätigt. Die Schweißerprüfung oder das Zertifikat muss in der Regel alle drei Jahre erneuert werden, um die Aktualität und die Qualität der Schweißfertigkeiten zu gewährleisten. Die Schweißerprüfung oder das Zertifikat kann bei verschiedenen Institutionen wie der Industrie- und Handelskammer, dem Deutschen Verband für Schweißen und verwandte Verfahren oder dem TÜV erworben werden.
Wie sieht die Zukunft des Laserschweißens aus?
Das Laserschweißen ist ein zukunftsweisendes Schweißverfahren, das in vielen Branchen und Bereichen eingesetzt wird und wird. Die Nachfrage nach qualifizierten und erfahrenen Laserschweißern ist daher hoch und wird voraussichtlich weiter steigen. Das Laserschweißen bietet viele Möglichkeiten für die berufliche Entwicklung und die Spezialisierung, zum Beispiel in den Bereichen der Automobilindustrie, der Luft- und Raumfahrt, der Medizintechnik, der Energieerzeugung oder der Kunst und Kultur. Das Laserschweißen ist auch ein dynamisches und innovatives Schweißverfahren, das ständig weiterentwickelt und verbessert wird, um neue Herausforderungen und Anforderungen zu erfüllen. Das Laserschweißen erfordert daher eine kontinuierliche Weiterbildung und Anpassung, um auf dem neuesten Stand der Technik und des Wissens zu bleiben.