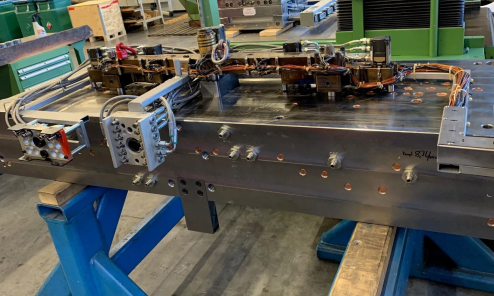
Die Geschichte des Formenbaus: Ein Blick in die Vergangenheit
Die Geschichte des Formenbaus: Ein Blick in die Vergangenheit
Von der Handarbeit bis zur digitalen Fertigung: Der Wandel des Formenbaus im Laufe der Zeit.
Einleitung: Wie hat sich der Formenbau im Laufe der Geschichte entwickelt? Von primitiven Methoden in der Antike bis hin zur modernen CNC-Technologie und 3D-Druck, die Evolution des Formenbaus spiegelt auch die Entwicklung der Menschheit und ihrer Technologie wider. In diesem Artikel werden wir einen genaueren Blick auf diesen spannenden Weg werfen.
Hauptteil: Der Formenbau hat seine Wurzeln in der Antike, wo handgeschnitzte Formen aus Holz, Stein oder Ton verwendet wurden, um verschiedene Produkte, meist Keramik, herzustellen. Diese Methoden erforderten ein hohes Maß an Handfertigkeit und Erfahrung, und die resultierenden Produkte waren oft Unikate.
Mit dem Beginn der industriellen Revolution im 18. und 19. Jahrhundert veränderte sich der Formenbau jedoch grundlegend. Mit der Einführung von Maschinen und der Entdeckung neuer Materialien wie Stahl und Aluminium begann die Ära des Maschinenbaus. Formen wurden nun mit Maschinen präzise hergestellt, was zu einer höheren Produktionsrate und gleichbleibenden Qualität führte.
Im 20. Jahrhundert erlebte der Formenbau durch die Einführung von Kunststoffen und der Entwicklung von Spritzgießverfahren eine weitere Revolution. Die Fähigkeit, komplexe Formen mit hoher Präzision in großen Mengen herzustellen, führte zu einer Explosion in der Produktion von Konsumgütern, von Spielzeug bis zu Autoteilen.
In den letzten Jahrzehnten hat die Einführung von Computer-Aided Design (CAD) und Computer-Aided Manufacturing (CAM) den Formenbau erneut verändert. Diese digitalen Technologien ermöglichen es Ingenieuren und Designern, Formen mit einer Präzision zu entwerfen und herzustellen, die zuvor undenkbar war. Zudem hat der 3D-Druck den Weg für Prototypen und sogar endgültige Produkte geebnet, wodurch der Formenbau noch flexibler und schneller wurde.
FAQ Sektion: 1. Wie hat sich die Materialwahl im Laufe der Zeit verändert? In der Antike wurden vor allem natürliche Materialien wie Holz, Stein und Ton verwendet. Mit der industriellen Revolution kamen Metalle wie Stahl und Aluminium hinzu. Das 20. Jahrhundert brachte Kunststoffe in den Formenbau ein, und heute experimentieren wir mit verschiedenen Verbundstoffen und sogar biologisch abbaubaren Materialien.
2. Was sind die Hauptvorteile der digitalen Technologie im Formenbau? Digitale Technologien wie CAD und CAM ermöglichen eine hohe Präzision, Effizienz und Flexibilität. Designs können leicht geändert, getestet und optimiert werden, und der eigentliche Herstellungsprozess kann automatisiert und beschleunigt werden.
3. Was kann man von der Geschichte des Formenbaus für die Zukunft erwarten? Die Geschichte lehrt uns, dass der Formenbau sich ständig weiterentwickelt, um den Anforderungen der Zeit gerecht zu werden. Mit Fortschritten in der Technologie und Materialwissenschaft können wir in Zukunft noch präzisere, effizientere und umweltfreundlichere Formenbauverfahren erwarten.
Zusammenfassung: Der Formenbau hat im Laufe der Zeit erhebliche Veränderungen erfahren, von der manuellen Handarbeit in der Antike bis zur digitalen Fertigung heute. Diese Evolution spiegelt die technologischen Fortschritte und den Erfindergeist der Menschheit wider.
Fazit: Der Formenbau ist ein Spiegelbild der technologischen Entwicklung und des Fortschritts. Wie in vielen Bereichen des Maschinenbaus treiben Neugier und Innovationskraft die Branche voran, um immer bessere, effizientere und nachhaltigere Lösungen zu finden. Es bleibt spannend zu beobachten, wie sich der Formenbau in der Zukunft weiterentwickeln wird.