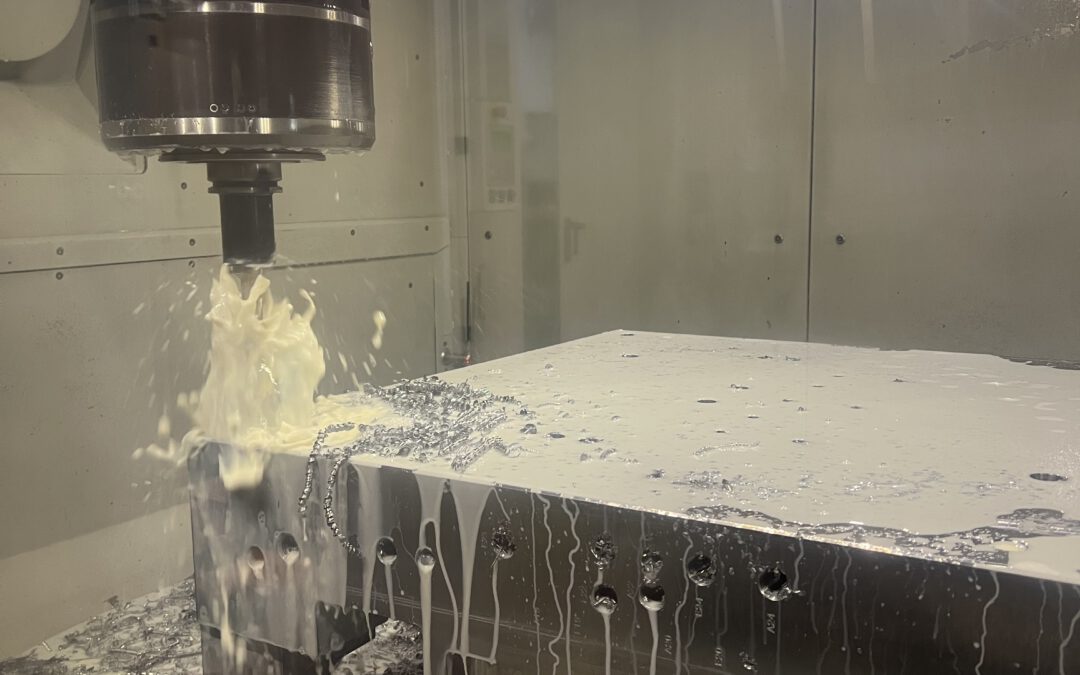
Aktuelle Trends im Maschinenbau
Aktuelle Trends im Maschinenbau
Die Zukunft im Blick: Aktuelle Trends im Maschinenbau
Untertitel: Von Automatisierung bis hin zu nachhaltigen Praktiken: Wie sich die Welt des Maschinenbaus wandelt
Einleitung: In einer Welt, die sich rasch verändert, wie bleibt der Maschinenbau relevant und fortschrittlich? Die Antwort liegt in der Anpassung an neue Trends und Technologien, die nicht nur die Effizienz und Produktivität steigern, sondern auch nachhaltige und zukunftsorientierte Praktiken fördern. In diesem Artikel werfen wir einen Blick auf einige der wichtigsten Trends im Maschinenbau, die Formenbauer und Maschinenbauer beeinflussen und leiten werden.
Hauptteil:
-
Automatisierung und Robotik: Die Automatisierung hat sich von einem Luxus zu einer Notwendigkeit gewandelt, mit Robotern, die nun komplexe Aufgaben übernehmen und die Effizienz steigern.
-
Künstliche Intelligenz (KI) und Maschinelles Lernen (ML): KI und ML ermöglichen es Maschinen, von Daten zu lernen und Prozesse zu optimieren, was zu besserer Qualität und geringeren Kosten führt.
-
Nachhaltigkeit und Ressourceneffizienz: Der Druck, umweltfreundliche Praktiken zu adoptieren, steigt, und Maschinenbauer suchen nach Wegen, um Energie zu sparen und Abfall zu reduzieren.
-
Additive Fertigung: Der 3D-Druck ermöglicht die schnelle Prototypenentwicklung und die Fertigung komplexer Bauteile mit weniger Materialverschwendung.
-
Internet der Dinge (IoT) und Industrie 4.0: Die Vernetzung von Maschinen und Systemen ermöglicht eine bessere Datenanalyse und Prozessoptimierung in Echtzeit.
FAQ Sektion:
-
Wie wirkt sich die Automatisierung auf die Arbeitsplätze aus? Automatisierung kann Arbeitsplätze verlagern, schafft aber auch neue Möglichkeiten für höher qualifizierte Positionen.
-
Welche Rolle spielen KI und ML im modernen Maschinenbau? KI und ML können bei der Vorhersage von Wartungsbedarf und bei der Optimierung von Design und Fertigungsprozessen helfen.
-
Wie können Unternehmen die Nachhaltigkeit in ihre Praktiken integrieren? Durch die Auswahl umweltfreundlicher Materialien und die Minimierung von Abfall und Energieverbrauch.
Zusammenfassung: Die Welt des Maschinenbaus befindet sich in einer spannenden Phase des Wandels und der Innovation. Durch die Einführung neuer Technologien und die Umsetzung nachhaltiger Praktiken können Formenbauer und Maschinenbauer ihre Prozesse optimieren und sich auf eine erfolgreiche Zukunft vorbereiten.
Fazit: Die Anpassung an aktuelle Trends ist nicht nur für den Fortschritt unerlässlich, sondern auch für die Sicherstellung der Relevanz in einer sich ständig weiterentwickelnden Industrie. Mit einem offenen Blick für Innovation und einer Verpflichtung zur kontinuierlichen Verbesserung können Maschinenbauer ihre Ziele erreichen und einen positiven Einfluss auf die Gesellschaft und die Umwelt haben.