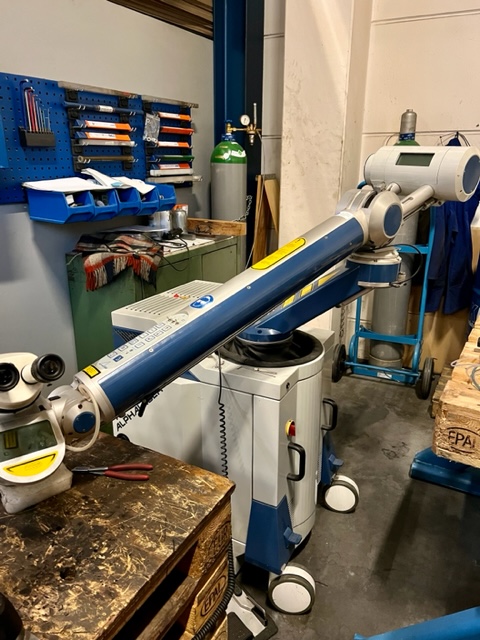
Die Rolle von Laserschweißen in der Kunststoffindustrie
Revolution im Formenbau: Laserschweißen in der Kunststoffindustrie
Neueste Dimensionen der Effizienz und Qualität durch Lasertechnologie
Inhaltsverzeichnis
- Einleitung
- Grundlagen des Laserschweißens
- Anwendungsbereiche im Formenbau und Spritzguss
- Vorteile des Laserschweißens in der Kunststoffindustrie
- Integration in bestehende Produktionsprozesse
- Fallstudien und Erfolgsbeispiele
- Technologische Innovationen und Trends
- Herausforderungen und Lösungsansätze
- Nachhaltigkeitsaspekte des Laserschweißens
- Zukunftsperspektiven und Ausblick
- FAQ Sektion
- Zusammenfassung
- Fazit
- Call to Action
1. Einleitung
Die Kunststoffindustrie steht vor einer bahnbrechenden Veränderung durch die Einführung des Laserschweißens. Diese Technologie verspricht, die Effizienz, Präzision und Qualität in der Produktion zu revolutionieren. In diesem Artikel beleuchten wir, wie das Laserschweißen den Formenbau und Spritzguss transformiert und welche Vorteile es mit sich bringt.
2. Grundlagen des Laserschweißens
Laserschweißen ist ein fortschrittliches Verfahren, das konzentrierte Laserstrahlen nutzt, um Materialien mit hoher Präzision zu verbinden. Im Vergleich zu traditionellen Schweißmethoden bietet es eine unübertroffene Genauigkeit und Kontrolle, was es ideal für die komplexe Geometrie im Formenbau macht.
3. Anwendungsbereiche im Formenbau und Spritzguss
In der Kunststoffindustrie findet das Laserschweißen Anwendung in der Herstellung von Präzisionsteilen, insbesondere im Formenbau und Spritzguss. Durch seine Fähigkeit, feine Details zu bearbeiten, ermöglicht es die Produktion von Komponenten mit hoher Genauigkeit und Konsistenz.
4. Vorteile des Laserschweißens in der Kunststoffindustrie
Das Laserschweißen steigert nicht nur die Effizienz und Qualität, sondern bietet auch eine verbesserte Flexibilität in der Fertigung. Es ermöglicht schnelle Designänderungen, reduziert Produktionszeiten und minimiert Materialverschwendung, was zu erheblichen Kosteneinsparungen führt.
5. Integration in bestehende Produktionsprozesse
Die Integration des Laserschweißens in bestehende Produktionslinien erfordert anfängliche Investitionen in Ausrüstung und Schulung. Jedoch amortisieren sich diese Investitionen durch die gesteigerte Produktionseffizienz und verbesserte Produktqualität schnell.
6. Fallstudien und Erfolgsbeispiele
Verschiedene Fallstudien zeigen, dass Unternehmen, die Laserschweißtechnologien implementieren, signifikante Verbesserungen in der Produktionseffizienz und Produktqualität erleben. Diese Erfolgsbeispiele dienen als Inspiration und Wegweiser für andere in der Branche.
7. Technologische Innovationen und Trends
Die ständige Weiterentwicklung des Laserschweißens, einschließlich der Automatisierung und der Integration von KI, deutet auf eine helle Zukunft für diese Technologie in der Kunststoffindustrie hin. Diese Innovationen versprechen eine noch größere Effizienz und Flexibilität.
8. Herausforderungen und Lösungsansätze
Trotz der vielen Vorteile stehen Unternehmen vor Herausforderungen wie der anfänglichen Kapitalinvestition und dem Bedarf an spezialisierten Fachkräften. Lösungen hierfür sind Partnerschaften mit Technologieanbietern und Investitionen in Mitarbeiterausbildung.
9. Nachhaltigkeitsaspekte des Laserschweißens
Das Laserschweißen ist nicht nur effizient, sondern auch umweltfreundlich. Es reduziert den Energieverbrauch und Abfall, was es zu einer nachhaltigen Option in der Kunststoffverarbeitung macht.
10. Zukunftsperspektiven und Ausblick
Die Zukunft des Laserschweißens in der Kunststoffindustrie ist vielversprechend. Es wird erwartet, dass diese Technologie eine Schlüsselrolle in der weiteren Automatisierung und Effizienzsteigerung spielen wird.
11. FAQ Sektion
- Frage: Kann das Laserschweißen für alle Kunststoffe verwendet werden?
- Antwort: Ja, es ist für die meisten Kunststoffarten geeignet, wobei die spezifischen Eigenschaften des Materials berücksichtigt werden müssen.
- Frage: Wie verändert das Laserschweißen die Produktionskosten?
- Antwort: Es führt zu einer langfristigen Kostensenkung durch Effizienzsteigerung und Materialersparnis.
(Weitere Fragen und Antworten in der vollständigen Version)
12. Zusammenfassung
Das Laserschweißen stellt eine revolutionäre Veränderung in der Kunststoffindustrie dar, die den Formenbau und Spritzguss in Bezug auf Effizienz, Qualität und Nachhaltigkeit neu definiert.
13. Fazit
Die Implementierung von Laserschweißtechnologien ist ein entscheidender Schritt für Unternehmen in der Kunststoffindustrie, die ihre Produktionsprozesse modernisieren und ihre Marktposition stärken wollen.
14. Call to Action
Interessiert an weiteren Informationen zum Laserschweißen oder möchten Sie erfahren, wie diese Technologie Ihrem Unternehmen nutzen kann? Kontaktieren Sie uns für eine persönliche Beratung oder registrieren Sie sich für unser nächstes Webinar zum Thema.