Spritzguss-Formenbau: Wichtige Methoden – Fräsen, Erodieren, 3D-Druck
Methoden im Formenbau für Spritzguss: Ein Überblick
Inhaltsverzeichnis
-
Einleitung
-
Konventionelle Zerspanung im Formenbau
-
HSC-Fräsen (High-Speed Cutting) im Werkzeugbau
-
Erodieren im Formenbau (Senkerosion & Drahterosion)
-
Additive Fertigung (3D-Druck) für Spritzgussformen
-
Hybrid-Ansätze im Spritzguss-Formenbau
-
Fazit
Einleitung
Im Werkzeug- und Formenbau – speziell bei der Herstellung von Spritzgussformen – kommen heute unterschiedlichste Methoden und Fertigungsverfahren zum Einsatz. Technische Entscheider, Entwickler und Einkäufer stehen vor der Herausforderung, aus einer Vielzahl an Verfahren die optimale Kombination für ein gegebenes Formwerkzeug auszuwählen. Klassische konventionelle Zerspanung, moderne HSC-Frästechnik, präzises Erodieren, fortschrittliche additive Fertigung (3D-Druck) und Hybrid-Ansätze ergänzen einander, um immer schneller hochwertige Spritzguss-Werkzeuge herzustellen. Jedes Verfahren bietet spezifische Stärken – keine einzelne Methode erfüllt jedoch alle Anforderungen alleine. In dieser Einleitung geben wir einen Überblick, bevor wir im Hauptteil die wichtigsten Methoden im Spritzguss-Formenbau technisch beleuchten.
Gegenüberstellung typischer Prozessschritte im Spritzguss-Formenbau: konventioneller Prozess (links) vs. additiver Prozess (Mitte) vs. Hybrid-Prozess (rechts). Bei Hybridansätzen werden z. B. konventionell gefräste Formgrundkörper und additiv gefertigte Einsätze kombiniert und anschließend gemeinsam nachbearbeitet und montiert.
Wie Abbildung 1 verdeutlicht, unterscheiden sich konventionelle, additive und hybride Herstellungswege deutlich in der Prozesskette. Konventionelle Prozesse basieren auf spanender Bearbeitung (Fräsen, Bohren, Drehen) und ergänzenden Verfahren wie Erodieren, gefolgt von Nacharbeit (Polieren, Montage und Probelauf). Additive Prozesse (Rapid Tooling) bauen Formeinsätze schichtweise im 3D-Druck auf und erfordern anschließend eine zerspanende Nachbearbeitung zur Maß- und Oberflächenoptimierung, bevor die Form in Betrieb gehen kann. Hybride Ansätze kombinieren beide Welten: Während Grundformen konventionell gefertigt werden, entstehen komplexe Einsätze mit konturnaher Kühlung additiv und werden anschließend passgenau eingepasst. Dieses Hybrid Molding erschließt Vorteile aller Verfahren, erhöht aber auch die Planungsanforderungen, da mehrere Fertigungsschritte parallel koordiniert werden müssent.
Im Folgenden werden die einzelnen Methoden – von der klassischen Zerspanung über HSC-Fräsen und Erodieren bis hin zu additiven und hybriden Verfahren – ausführlich dargestellt. Dabei beleuchten wir Funktionsweise, Vorteile und Nachteile sowie die typische Verwendung der Methoden bei der Herstellung von Formwerkzeugen für den Spritzguss.
Konventionelle Zerspanung im Formenbau
Die konventionelle Zerspanung bildet seit jeher das Rückgrat im Formenbau. Darunter fallen klassische abtragende Fertigungsverfahren wie Fräsen, Drehen und Bohren, mit denen Formstahl-Blöcke in die gewünschte Form gebracht werden. Modernste CNC-Bearbeitungszentren (heute meist 3- bis 5-Achsen) ermöglichen eine präzise Bearbeitung der Formkonturen. Zunächst wird häufig das Formen-Grundgerüst durch CNC-Fräsen aus dem vollen Material herausgearbeitet (Grobbearbeitung). Auch Bohrungen für Auswerfer, Kühlkanäle und Befestigungen entstehen in diesem Schritt. Für rotationssymmetrische Bauteile (z. B. Kernstifte oder Buchsen) kommt das Drehen zum Einsatz.
Vorteile: Die konventionelle Zerspanung ist universell einsetzbar und erzielt in Kombination mit nachträglichem Polieren sehr hohe Oberflächengüten und Maßgenauigkeiten. Über Jahrzehnte optimierte Maschinen und Schneidwerkzeuge ermöglichen zuverlässige Prozesse und reproduzierbare Qualität. Durch Erfahrung und stetige Weiterentwicklung können selbst komplexe Geometrien schrittweise herausgearbeitet werden. Außerdem lassen sich gehärtete Werkzeugstähle heute dank spezieller Fräser und Strategien ebenfalls spanend bearbeiten (z. B. Hartfräsen).
Nachteile: Limitierend für rein zerspanende Verfahren ist die Geometriefreiheit. Sehr enge Ecken, tiefe schmale Kavitäten oder Hinterschnitte kann der Fräser nicht erreichen. Solche Bereiche müssen oft in separaten Operationen (z. B. per Erodieren) erzeugt werden. Zudem steigen bei wachsender Bauteilkomplexität oft die Fertigungszeiten und -kosten überproportional an, da viele einzelne Fräsoperationen und Werkzeugwechsel nötig sind. Mit herkömmlichem Fräsen allein ist es also schwierig, komplexe Spritzgussformen schnell und kosteneffizient herzustellen, ohne Kompromisse bei der Detailgenauigkeit einzugehen. In der Praxis wird die konventionelle Zerspanung daher meist mit anderen Methoden kombiniert, um beste Ergebnisse zu erzielen.
HSC-Fräsen (High-Speed Cutting) im Werkzeugbau
Eine bedeutende Weiterentwicklung der konventionellen Frästechnik stellt das HSC-Fräsen (High-Speed Cutting) dar. Hierbei wird mit sehr hohen Schnittgeschwindigkeiten und Vorschüben gearbeitet, oft auf steifen 5-Achs-Maschinen mit hochdrehenden Spindeln. Die Idee: Durch hohe Umdrehungszahlen (20.000–40.000 U/min und mehr) und kleine Zustelltiefen können selbst harte Werkstoffe extrem schnell und zugleich präzise gefräst werden. Das ermöglicht deutlich höhere Materialabtragraten und feinere Oberflächen als beim Standardfräsen. In vielen Formenbau-Betrieben hat sich HSC daher als Alternative oder Ergänzung zum Erodieren etabliert.
Vorteile: Gegenüber dem Senkerodieren können mit HSC-Fräsen die Bearbeitungszeiten drastisch reduziert werden. Es wird berichtet, dass HSC eine um bis zu 30 % höhere Abtragsleistung und 5–10 fach höhere Vorschubgeschwindigkeiten erlaubt. Dadurch sinken die Fertigungszeiten für formgebende Konturen deutlich. Dank minimaler Schnittkräfte lassen sich sogar gehärtete Stähle (HRC > 50) bearbeiten, ohne das Werkstück zu beschädigen. Die erreichbaren Oberflächengüten sind exzellent – oft ist nach dem Schlichten kein manuelles Polieren mehr nötig. Ein weiterer Vorteil: Das Fräsen ist im Gegensatz zum Erodieren nicht auf leitfähige Materialien beschränkt und erzeugt keine elektrolytische Weißschicht, die aufwändig entfernt werden müsste. HSC eignet sich besonders für filigrane Konturen, dünnwandige Formen und Freiformflächen, die früher zwangsweise erodiert werden mussten.
Nachteile: Trotz aller Stärken kann HSC-Fräsen das Erodieren nicht komplett ersetzen. Bei sehr tiefen, schlanken Kavitäten stoßen auch hochdynamische Fräser an ihre Grenzen, da extrem lange Werkzeuge nötig wären. Hier bleibt die Erosion im Vorteil. Zudem sind HSC-Maschinen und -Werkzeuge eine Investition – nicht jeder Formenbauer verfügt über passende Ausstattung. Die Technologie erfordert hochpräzise Programmierung und erfahrene Bediener, um Schwingungen und Werkzeugverschleiß zu minimieren. In der Praxis wird HSC daher gezielt dort eingesetzt, wo es den größten Nutzen bringt (z. B. schnelle Bearbeitung von Elektroden, feine Gravuren oder Einsätze), während andere Bereiche weiterhin erodiert oder konventionell gefräst werden. Wichtig ist, die Wahl des Verfahrens stets an Geometrie und Toleranzanforderungen auszurichten.
Erodieren im Formenbau (Senkerosion & Drahterosion)
Das Erodieren – insbesondere die Senkerosion – ist ein klassisches Präzisionsverfahren im Formenbau. Bei der Senkerosion wird mittels elektrischer Entladungen Material punktuell abgetragen: Eine formgebende Elektrode (aus Kupfer oder Grafit) wird in die Werkstückoberfläche eingesenkt und brennt die gewünschte Form in den Stahl. Dieses Verfahren ist prädestiniert für tiefe, schmale Konturen, scharfe Ecken und komplexe 3D-Formen, die mit Fräsen kaum erreichbar wären. Auch Hinterschnitte und feine Rippen können erodiert werden, sofern die Elektrode entsprechend gestaltet ist. Neben der Senkerosion wird im Formenbau auch die Drahterosion (ein gespannter Messingdraht schneidet Konturen) eingesetzt, etwa um Konturplatten oder Durchbrüche mit höchster Präzision aus dem Vollmaterial zu schneiden.
Vorteile: Erodierverfahren bieten eine enorme Formfreiheit für harte Werkstoffe. Selbst in große Materialstärken lassen sich äußerst feine Strukturen mit extremer Genauigkeit einbringen. Die erzielbaren Oberflächengüten sind hervorragend – Rauheitswerte bis zu Ra 0,4 μm und Toleranzen im Mikrometerbereich sind erreichbar. Senkerodieren ermöglicht zudem absolut rechtwinklige Innenkanten und schmale Spalte, was beim Fräsen wegen des Werkzeugradius nicht möglich ist. Drahterodieren schneidet komplexe Umrisse mit minimalem Grat. Kurz: Überall dort, wo mechanische Bearbeitung an technologische Grenzen stößt, spielt Erodieren seine Stärke aus.
Nachteile: Die Kehrseite sind vergleichsweise lange Bearbeitungszeiten und höhere Kosten pro Eingriff. Das Erodieren ist ein langsamer Prozess – insbesondere tiefe Kavitäten können Stunden bis Tage benötigen, da der Materialabtrag schichtweise erfolgt. Zudem muss zunächst für jede zu erodierende Form eine Elektrode gefertigt werden (häufig selbst per CNC-Fräsen oder 3D-Druck), was den Aufwand erhöht. Die Materialvielfalt ist eingeschränkt: Nur elektrisch leitfähige Materialien können erodiert werden, was in der Praxis jedoch meist unproblematisch ist, da Spritzgusswerkzeuge aus Stahl oder Kupfer-Beryllium bestehen. Schließlich entsteht beim Erodieren eine dünne beeinträchtigte Randzone (Rekast-Schicht), die je nach Anwendung durch Polieren oder Anlassen entfernt werden muss. Insgesamt ist die Erosion also hochpräzise, aber zeit- und kostenintensiv. Oft wird sie gezielt für diejenigen Formbereiche eingesetzt, die andere Verfahren nicht zufriedenstellend abbilden können (z. B. scharfe Innenecken, tiefe Kühlkanäle, feinste Strukturen). Wo immer möglich, versuchen Formenbauer heute, auf schnellere Verfahren wie HSC auszuweichen – außer die Kontur erfordert zwingend eine Erodierung.
Additive Fertigung (3D-Druck) für Spritzgussformen
Die additive Fertigung hält als vergleichsweise neues Werkzeug zunehmend Einzug in den Spritzguss-Formenbau. Unter dem Stichwort „Rapid Tooling“ werden beispielsweise Formeinsätze mittels 3D-Druck hergestellt, die in Spritzgusswerkzeuge integriert werden. Insbesondere metallische additive Verfahren wie das Selektive Laserschmelzen (SLM) ermöglichen es, Stahl-Formeinsätze schichtweise aufzubauen. Dadurch eröffnen sich Gestaltungsmöglichkeiten, die mit konventioneller Fertigung kaum realisierbar wären. Ein prominentes Beispiel ist die konturnahe Kühlung: Kühlkanäle können additiv in optimierter Geometrie direkt innerhalb des Formeinsatzes verlaufen, sehr nah an der Kavitätsoberfläche und in komplexen 3D-Schleifen, was die Kühlleistung und damit die Zykluszeit im Spritzguss erheblich verbessert. Auch sehr filigrane oder bionische Strukturen lassen sich durch 3D-Druck erzeugen, die als konventionell gefräste Einsätze nicht denkbar wären.
Vorteile: Die größte Stärke additiver Verfahren ist die Freiheit in der Geometrie. Komplexität der Form spielt nahezu keine Rolle für den Herstellungsaufwand – das oft zitierte Prinzip „complexity for free“ kommt zum Tragen. Funktionen und Konturen, die in konventioneller Fertigung mehrere Bauteile erfordern würden, können in einem einzigen additiv gefertigten Formeinsatz vereint werden. Dies ermöglicht innovative Formkonzepte mit integrierten Funktionen (etwa Sensorik, Dämpfung oder Temperierung), die neue Möglichkeiten im Spritzguss eröffnen. Für Prototypen und Kleinserien können durch 3D-gedruckte Formeinsätze zudem sehr kurze Lieferzeiten erzielt werden – ohne dass erst eine vollständige Stahlform gefräst werden muss. Auch Reparaturen und Änderungen lassen sich in manchen Fällen additiv umsetzen, indem beschädigte Bereiche aufgedruckt und anschließend bearbeitet werden.
Nachteile: Trotz aller Vorteile steht die additive Fertigung im Formenbau noch vor Herausforderungen. Oberflächenqualität und Genauigkeit additiv gebauter Teile reichen meist nicht an CNC- oder EDM-gefertigte Oberflächen heran. Gedruckte Formeinsätze weisen eine raue Oberfläche und oft leichte Maßabweichungen auf, weshalb fast immer eine zerspanende Nachbearbeitung (Fräsen, Schleifen) nötig ist. Auch die Werkstoffeigenschaften können von konventionell vergütetem Werkzeugstahl abweichen – additiv gefertigte Metalle haben mitunter höhere Porosität oder anisotrope Eigenschaften, was die Dauerfestigkeit der Form beeinflusst. Ein weiterer limitierender Faktor sind die Bauzeiten und Kosten: Das Drucken metallischer Bauteile ist nach wie vor relativ langsam und energieintensiv. Große Formeinsätze aus Stahl im 3D-Druck herzustellen kann kostspielig sein und erfordert spezielle Maschinen. Additive Fertigung lohnt sich daher vor allem dort, wo ihr Mehrwert (z. B. drastisch verkürzte Kühlzeiten oder einzigartige Geometrien) die höheren Herstellkosten rechtfertigt. In vielen Fällen werden additive und konventionelle Verfahren kombiniert eingesetzt – genau hier kommen die Hybrid-Ansätze ins Spiel.
Hybrid-Ansätze im Spritzguss-Formenbau
Hybrid-Ansätze verbinden die Stärken unterschiedlicher Methoden, um optimale Ergebnisse im Spritzgussformenbau zu erzielen. In der Praxis bedeutet dies oft: Konventioneller Werkzeugbau + Additive Fertigung. Ein Beispiel ist das sogenannte Hybrid Molding.. Dabei werden konventionell hergestellte Formgrundkörper (z. B. gehärtete Stahlplatten mit Grundkontur, Aufnahmebohrungen, Auswerfer etc.) mit additiv gefertigten Einsätzen ergänzt, die besondere Geometrien oder Funktionen enthalten (etwa komplexe Kavitäten mit konturnahen Kühlkanälen). Diese verschiedenen Bauteile werden anschließend durch präzises Nacharbeiten (HSC-Fräsen, Schleifen, ggf. Erodieren der Feinmerkmale) auf Passmaß gebracht und zum fertigen Formwerkzeug montiert.Das Ergebnis sind hochleistungsfähige Spritzgussformen, die z. B. kürzere Zykluszeiten oder geringeren Verschleiß aufweisen, und die dennoch eine hohe Standzeit und Präzision bieten.
Ein hybrider Prozess erfordert zunächst zusätzlichen Konstruktionsaufwand. Bereits in der CAD-Phase muss entschieden werden, welche Formelemente mit welchem Verfahren gefertigt werden sollen. Der Konstrukteur teilt das Werkzeug in konventionelle und additive Komponenten auf und berücksichtigt etwaige Nacharbeit. Diese Vorgehensweise ist anspruchsvoll, bietet aber große Chancen: Parallelisierung und Spezialisierung der Verfahren. Während z. B. der Stahlgrundkörper gefräst und gehärtet wird, kann zeitgleich der komplizierte Einsatz im 3D-Druck entstehen. Beide Teile treffen dann in der Endmontage passgenau aufeinander. Durch solche Parallelprozesse beschleunigt sich die Gesamtfertigung trotz höherer Einzelkomplexität. Zudem erzielt der Hybridansatz Qualitätsvorteile: Konventionelle Teile bringen Robustheit und bewährte Eigenschaften, additive Teile liefern Kühlleistung und Gestaltungsfreiheit. Studien zeigen, dass hybride Prozessketten die Stückkosten bei komplexen Formen senken können.– etwa durch verkürzte Spritzgießzyklen aufgrund besserer Kühlung und geringeren Nacharbeitsaufwand.
Natürlich sind auch Grenzen zu beachten. Die Übergangsbereiche zwischen additivem Einsatz und konventioneller Form müssen nahtlos passen, was hohe Präzision bei beiden Teilprozessen erfordert. Die Materialverbindung (verschrauben, einkleben oder formschlüssig einpassen) muss zuverlässig und dicht sein (gerade bei Kühlkanälen kritisch). Außerdem steigen die Anforderungen an Planung, Personal und Maschinenpark: Ein Betrieb muss sowohl im klassischen Werkzeugbau als auch im 3D-Druck Expertise haben, um hybride Projekte erfolgreich umzusetzen. Trotz dieser Hürden gilt: Hybrid-Ansätze werden im Werkzeugbau als vielversprechender Weg gesehen, um innovative Spritzgusswerkzeuge schneller und wirtschaftlicher bereitzustellen. Sie kombinieren “das Beste aus beiden Welten” – und untermauern die eingangs erwähnte Erkenntnis, dass oft eine Kombination mehrerer Methoden zum Ziel führt.
Qualitativer Vergleich der Methoden in Schlüsselbereichen: Geometriefreiheit, Oberflächenqualität und Bearbeitungsgeschwindigkeit (★★★★★ = ausgezeichnet/sehr hoch, ★☆☆☆☆ = gering).Jede Methode zeigt unterschiedliche Stärken – komplexe Konturen gelingen bspw. am besten mit EDM oder additiv, während HSC in Tempo und Oberfläche punktet.
Fazit
Im Spritzgussformenbau gibt es eine Palette an Fertigungsmethoden, die sich gegenseitig ergänzen. Konventionelle Zerspanung bildet die Basis für robuste Formgrundstrukturen, HSC-Fräsen beschleunigt die Bearbeitung und liefert glänzende Oberflächen, Erodieren ermöglicht unerreichte Detailgenauigkeit in engen Bereichen, und additive Verfahren eröffnen eine neue Dimension der Gestaltungsfreiheit. Hybrid-Ansätze schließlich kombinieren diese Technologien, um die Vorteile zu vereinen und die jeweiligen Nachteile abzumildern.
Für den technischen Entscheider im Werkzeugbau heißt das: Die Wahl der Methode hängt von den Anforderungen des jeweiligen Formwerkzeugs ab – Geometrie, Toleranzen, Losgröße, Material und Budget spielen hinein. Oft führt eine clevere Kombination mehrerer Verfahren zum besten Ergebnis, sei es durch sequenzielle Prozessketten oder parallele Hybrid-Fertigung. Wichtig sind eine sorgfältige Planung und fundiertes Know-how über Formenbau-Methoden sowie deren Wechselwirkungen. Dann lassen sich Spritzguss-Formwerkzeuge mit hoher Effizienz, Qualität und Innovationsgrad herstellen. Der Formenbau der Zukunft wird weiterhin beide Welten – konventionell und additiv – nutzen, um immer komplexere Herausforderungen zu meistern und wettbewerbsfähig zu bleiben. Letztlich gilt: Methodenvielfalt im Formenbau ist kein Selbstzweck, sondern der Schlüssel, um für jede Form die optimalen Eigenschaften und die wirtschaftlichste Herstellung zu erzielen.
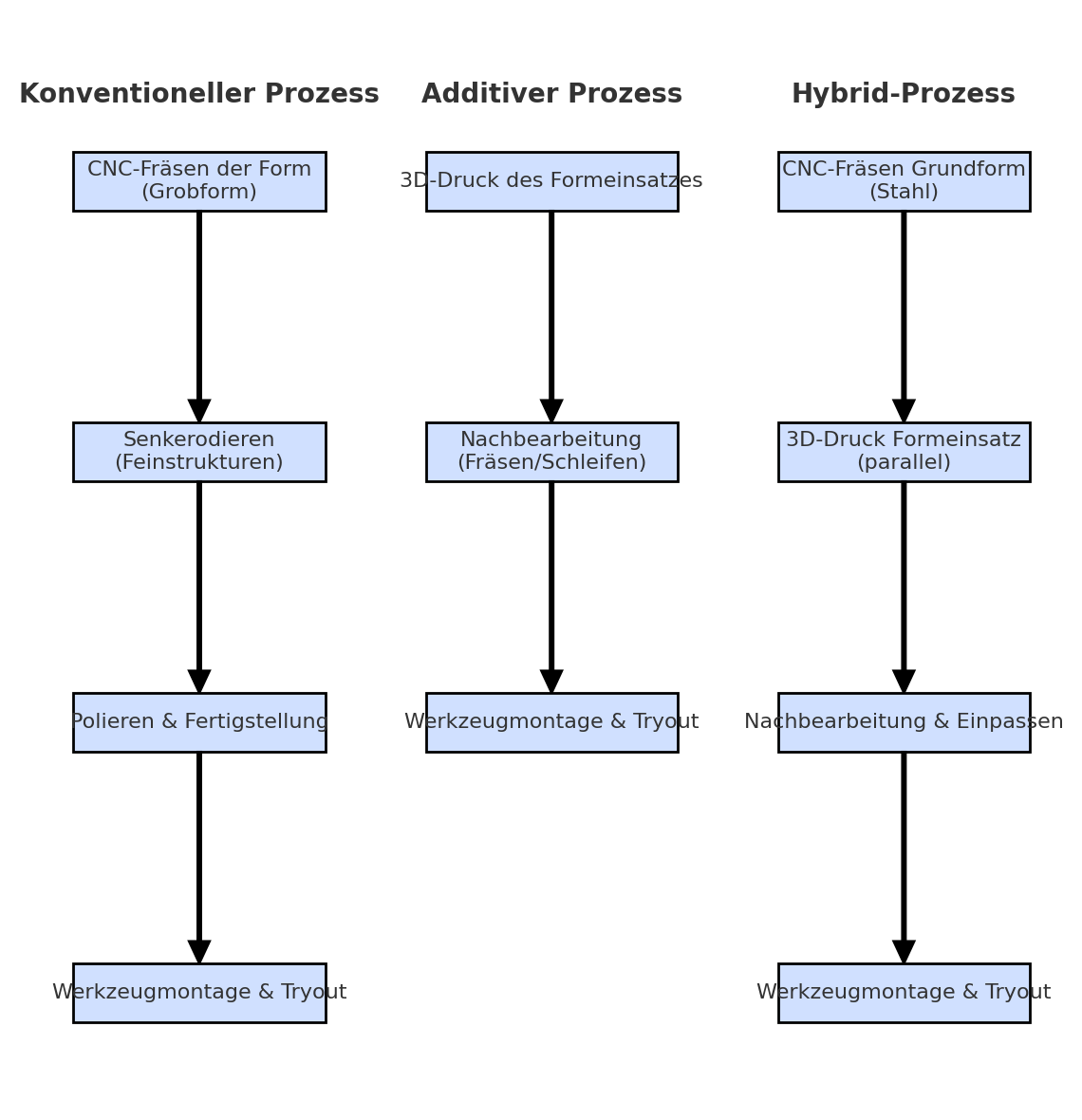