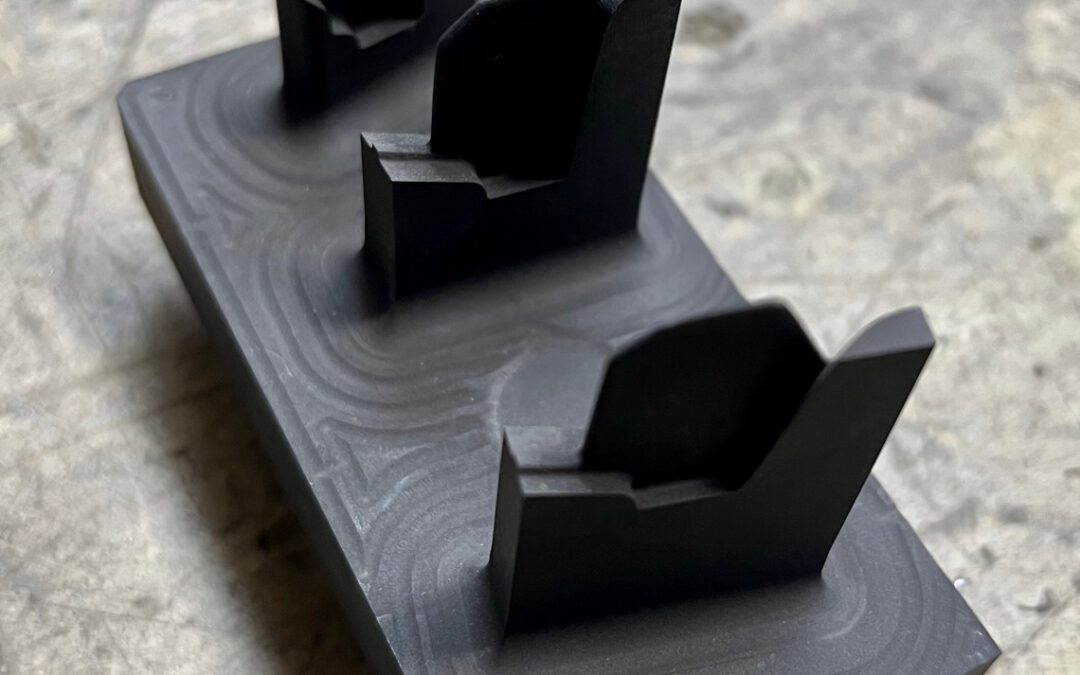
So wählen Sie das richtige Graphit für Ihre Senkerodierprojekte
So wählen Sie das richtige Graphit für Ihre Senkerodierprojekte
Das optimale Graphit für Ihre Senkerodierprojekte auswählen: Ein umfassender Leitfaden
Untertitel:
Navigieren Sie durch die Vielfalt an Graphitoptionen, um die Effizienz und Qualität Ihrer Formen- und Maschinenbauarbeiten zu steigern.
Einleitung
In der Welt des Formen- und Maschinenbaus ist die Wahl des richtigen Materials entscheidend für die Qualität und Effizienz der Fertigung. Eine häufig gestellte Frage ist: „Wie wähle ich das ideale Graphit für meine Senkerodierprojekte?“. Dieser Artikel bietet umfassende Einblicke und praktische Ratschläge zur Auswahl des optimalen Graphits, um die Leistung und Langlebigkeit Ihrer Werkzeuge und Maschinen zu maximieren.
Hauptteil
Graphitqualitäten und ihre Eigenschaften
Es gibt verschiedene Graphitqualitäten, die sich in Dichte, Korngröße, Festigkeit und elektrische Leitfähigkeit unterscheiden. Die Wahl der Graphitqualität hängt von den spezifischen Anforderungen Ihres Senkerodierprojekts ab. Hochdichtes Graphit mit feiner Korngröße bietet beispielsweise eine hervorragende Oberflächenqualität und Verschleißfestigkeit, ist jedoch kostenintensiver.
Faktoren, die die Wahl des Graphits beeinflussen
1. Komplexität des Projekts:
Die Komplexität des Werkstücks und die erforderliche Detailgenauigkeit beeinflussen die Wahl des Graphits. Für hochkomplexe Projekte ist ein feinkörniges Graphit ideal, da es präzise Details und feine Oberflächen liefert.
2. Budget:
Die Kosten des Graphits variieren je nach Qualität. Es ist entscheidend, ein Gleichgewicht zwischen den Kosten und den spezifischen Anforderungen Ihres Projekts zu finden.
3. Verfügbarkeit von Maschinen und Werkzeugen:
Die Art der verfügbaren Maschinen und Werkzeuge kann die Eignung bestimmter Graphitqualitäten beeinflussen. Stellen Sie sicher, dass Ihre Ausrüstung mit der gewählten Graphitqualität kompatibel ist.
FAQ Sektion
Frage: Wie beeinflusst die Korngröße des Graphits die Qualität des Endprodukts?
Je feiner die Korngröße, desto besser ist die Oberflächenqualität des Endprodukts. Feinkörniges Graphit ist jedoch anfälliger für Bruch und kann teurer sein.
Frage: Ist teureres Graphit immer die bessere Wahl?
Nicht unbedingt. Die Wahl des Graphits sollte auf den spezifischen Anforderungen des Projekts basieren. Manchmal kann ein kostengünstigeres Graphit die Anforderungen effizient erfüllen.
Frage: Wie kann ich die Leistung meines Graphits maximieren?
Die regelmäßige Wartung und Pflege des Graphits, einschließlich der Reinigung und Inspektion auf Risse oder Abnutzung, kann seine Leistung und Lebensdauer erheblich verlängern.
Zusammenfassung
Die Wahl des richtigen Graphits ist ein kritischer Faktor, der die Qualität, Effizienz und Wirtschaftlichkeit Ihrer Senkerodierprojekte beeinflusst. Durch die Berücksichtigung der Projektkomplexität, des Budgets und der verfügbaren Maschinen und Werkzeuge können Formenbauer und Maschinenbauer das ideale Graphit auswählen, um optimale Ergebnisse zu erzielen.
Fazit
Die technologische Landschaft des Formen- und Maschinenbaus entwickelt sich ständig weiter, und die Wahl des richtigen Graphits kann den Unterschied zwischen einem durchschnittlichen und einem außergewöhnlichen Endprodukt ausmachen. Durch ein vertieftes Verständnis der verschiedenen Graphitqualitäten und ihrer Anwendungen können Fachleute informierte Entscheidungen treffen, die zur Steigerung der Produktivität, Reduzierung der Betriebskosten und Verbesserung der Qualität ihrer Produkte führen. Die Investition in das richtige Graphit ist eine Investition in die Zukunft Ihres Unternehmens und der Branche als Ganzes.