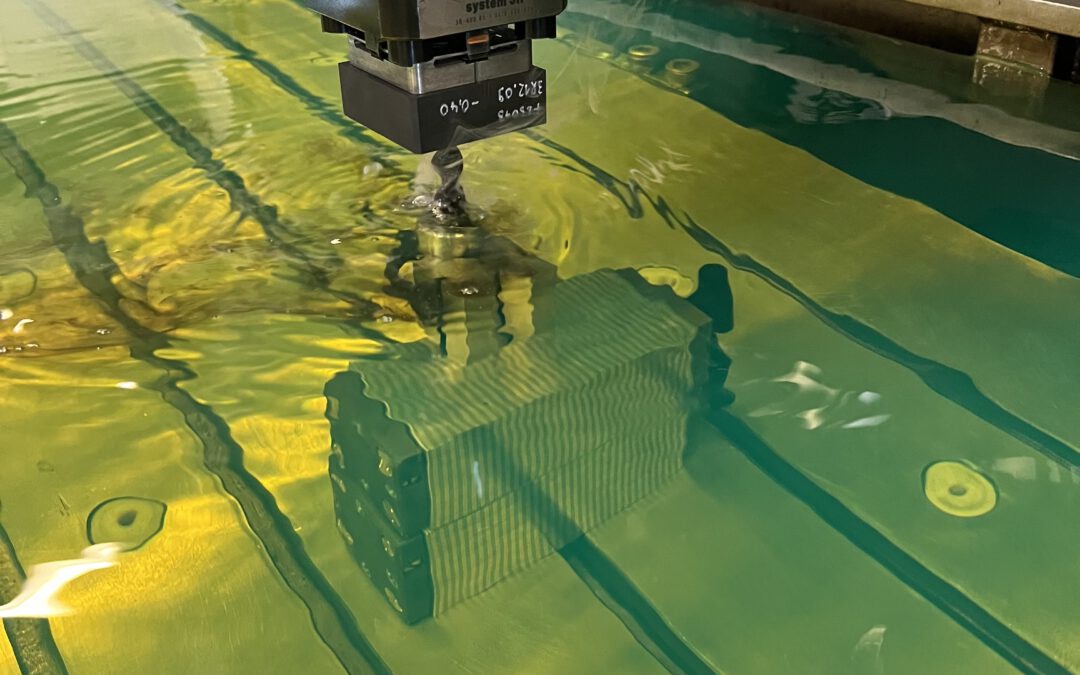
Auswerkungen von Senkerodieren auf die Werkstückintegrität
Auswerkungen von Senkerodieren auf die Werkstückintegrität
Optimierung der Werkstückintegrität durch Senkerodieren: Eine tiefgehende Analyse
Untertitel: Die fundamentale Rolle des Senkerodierens im Formenbau und Maschinenbau
Einleitung: Senkerodieren, ein nicht-traditionelles Fertigungsverfahren, hat sich als Schlüsseltechnologie in der modernen Fertigung etabliert. Doch wie wirkt sich dieses Verfahren auf die Integrität des Werkstücks aus, insbesondere im Bereich des Formenbaus und Maschinenbaus? Dieser Artikel zielt darauf ab, ein klares Verständnis über die Auswirkungen des Senkerodierens auf die Werkstückintegrität zu liefern und die damit verbundenen Vor- und Nachteile zu diskutieren.
Hauptteil: Senkerodieren ist ein elektrothermisches Verfahren, bei dem Material von einem Werkstück durch kontrollierte elektrische Entladungen entfernt wird. Dieses Verfahren wird oft für komplexe Formen und Materialien mit hoher Härte eingesetzt, wo traditionelle Fertigungsverfahren an ihre Grenzen stoßen.
-
Oberflächenintegrität: Das Senkerodieren beeinflusst die Oberflächenintegrität des Werkstücks erheblich. Durch die Erosion entsteht eine raue Oberfläche mit einer reichen Mikrostruktur, die eine gute Haftung für nachfolgende Beschichtungen ermöglicht.
-
Mikrorissbildung: Eine der größeren Herausforderungen beim Senkerodieren ist die Bildung von Mikrorissen. Diese Risse können die Festigkeit und die Lebensdauer des Werkstücks beeinträchtigen, jedoch können bestimmte Parameter des Senkerodierens angepasst werden, um diese Auswirkungen zu minimieren.
-
Wärmebehandlung: Die erzeugte Wärme beim Senkerodieren kann die Mikrostruktur des Materials verändern, was wiederum die mechanischen Eigenschaften des Werkstücks beeinflusst. Eine geeignete Nachbehandlung kann notwendig sein, um die gewünschten Eigenschaften zu erreichen.
FAQ Sektion:
- Was sind die Vorteile des Senkerodierens im Vergleich zu traditionellen Fertigungsverfahren?
- Wie kann die Oberflächenrauheit beim Senkerodieren kontrolliert werden?
- Welche Parameter des Senkerodierens beeinflussen die Werkstückintegrität am meisten?
Zusammenfassung: Senkerodieren bietet eine effiziente Lösung für die Herstellung von komplexen Formen und die Bearbeitung von hartem Material. Die Auswirkungen auf die Werkstückintegrität sind jedoch signifikant und müssen sorgfältig betrachtet und kontrolliert werden, um die gewünschten Ergebnisse zu erzielen.
Fazit: Die Auswirkungen des Senkerodierens auf die Werkstückintegrität sind vielfältig und können sowohl positiv als auch negativ sein. Durch ein tiefes Verständnis der Prozessparameter und der Materialreaktionen können Formenbauer und Maschinenbauingenieure das Potenzial des Senkerodierens voll ausschöpfen und die Leistung ihrer Produkte optimieren.
Dieser Blogartikel bietet einen professionellen Einblick in die Auswirkungen des Senkerodierens auf die Werkstückintegrität und stellt eine wertvolle Ressource für Fachleute im Formenbau und Maschinenbau dar.